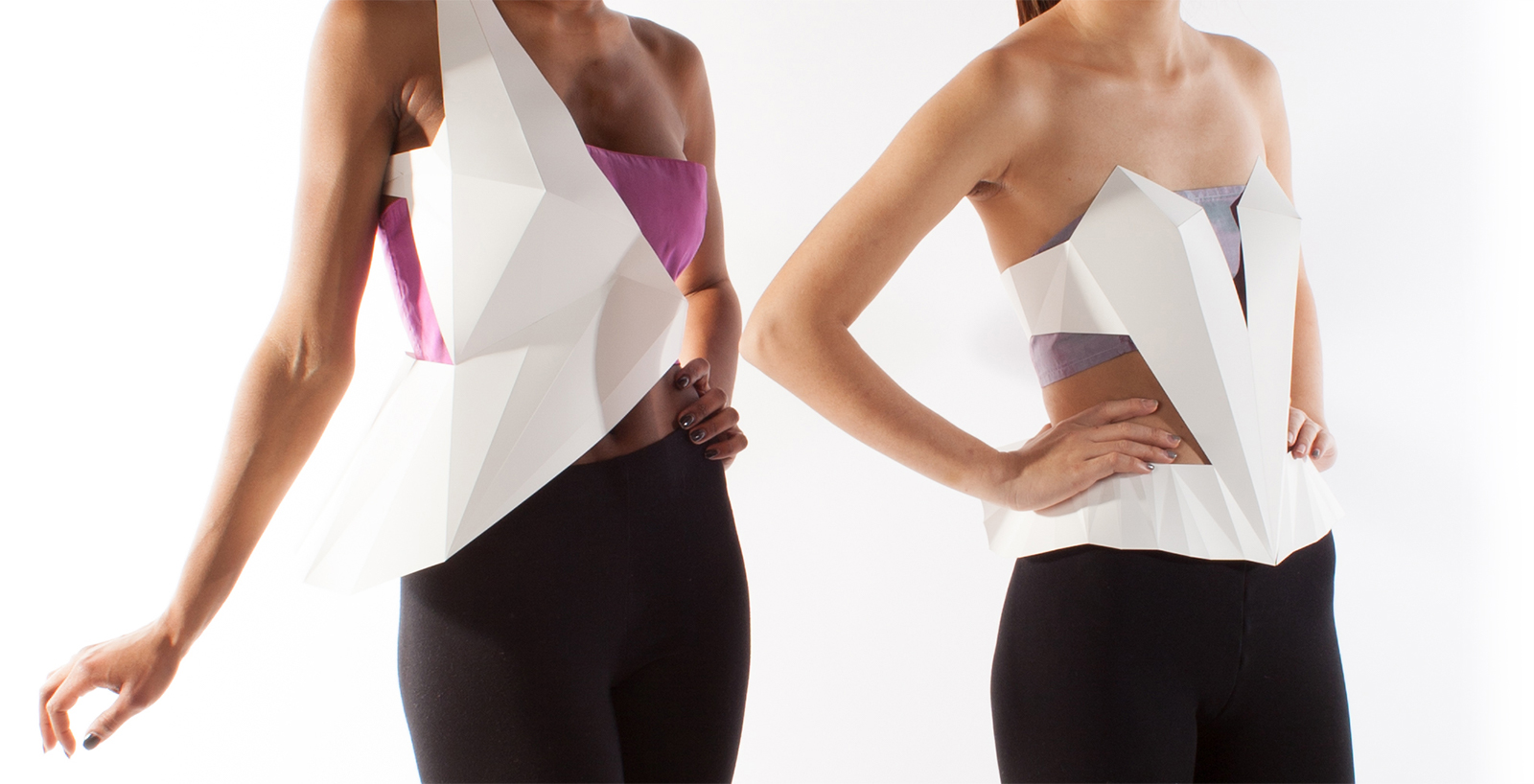
February 2015
Lustre
A fashion line with a new take on the production of clothes
We developed this collection with 2 goals in mind, create something beautiful and explore non-traditional approaches to get there. I’d like to think we accomplished both, though maybe not the way we first imagined.
We threw out the traditional production process of measure, cut, sew, fit and repeat in favor of more modern and adaptable processes. Leveraging digital design and fabrication techniques, primarily laser cutting and 3D printing and methods such as photogrammetry and computational design. The contrast of hand sewn silk garments versus digitally fabricated stark white tessellated garments leads us to Lustre’s concept. But first a huge shout out to 2 of my good friends Carolina Tamayo and Alyssa Hamilton, who I got the chance to work with on this collection.
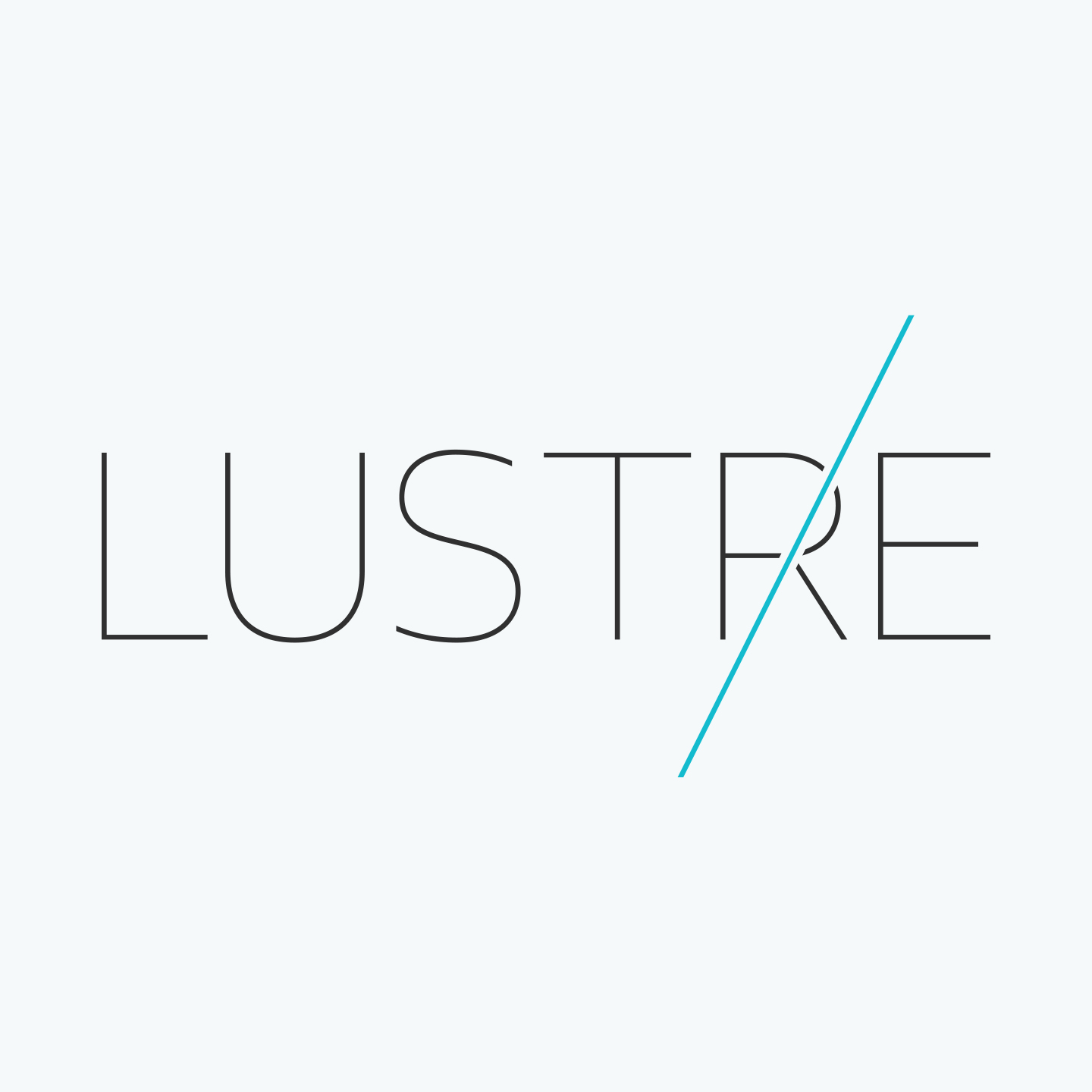
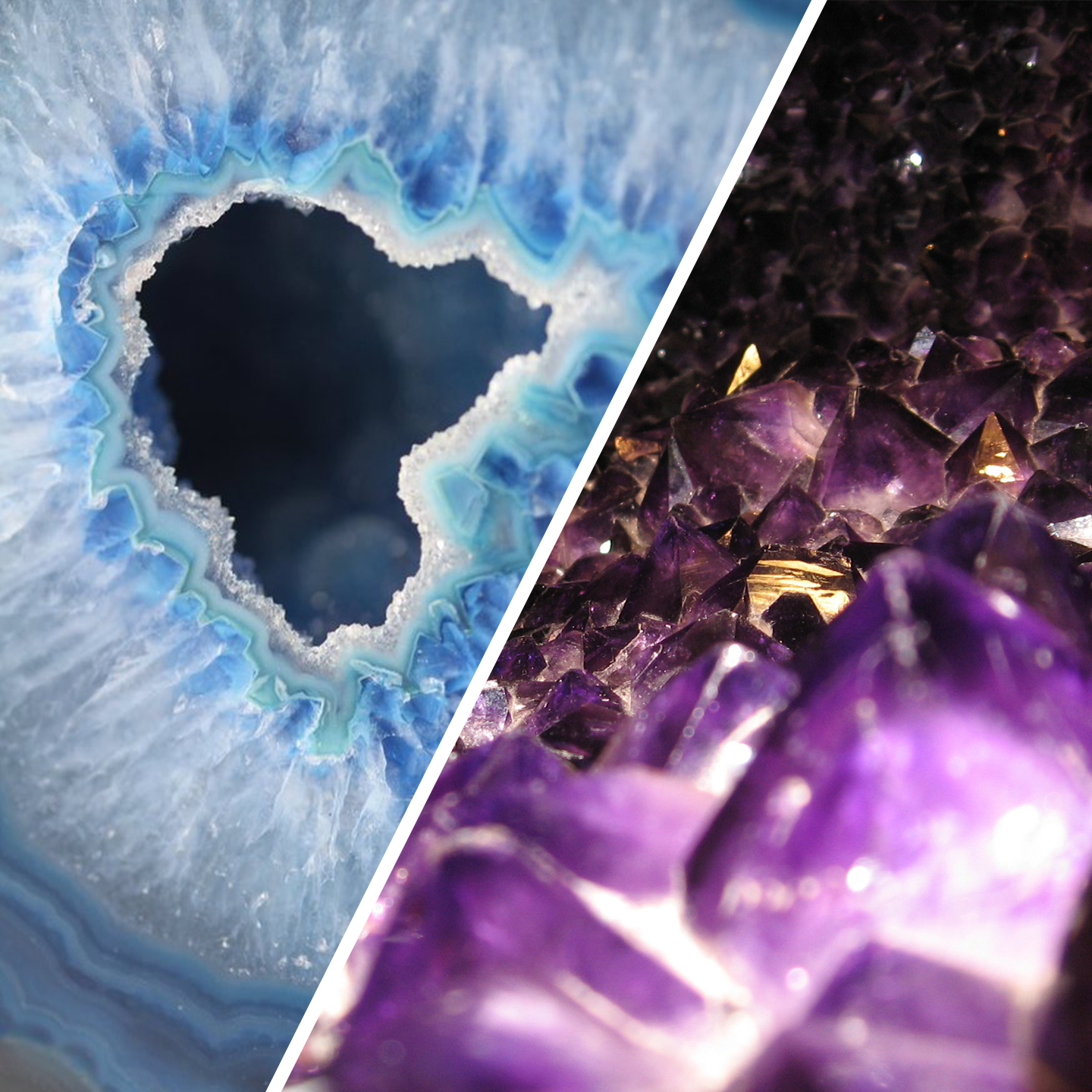
Lustre - the way light interacts with the surface of a crystal, rock, or mineral.
Our collection, Lustre, is inspired by geological formations, by the singular moment when a geode is split open, revealing colorful crystals within. With this in mind, the line showcases a natural progression of breaking down, perforating and shattering the rigid, rock-like structure of tessellated Yupo Paper, to reveal from underneath the free flowing fabrics of iridescent silk.
This concept is directly linked to the idea of clothing being a shell of the human form that socially delineates cultures and that only by breaking open this shell, and the prejudicial implications that go with it, can we reveal the true being within.
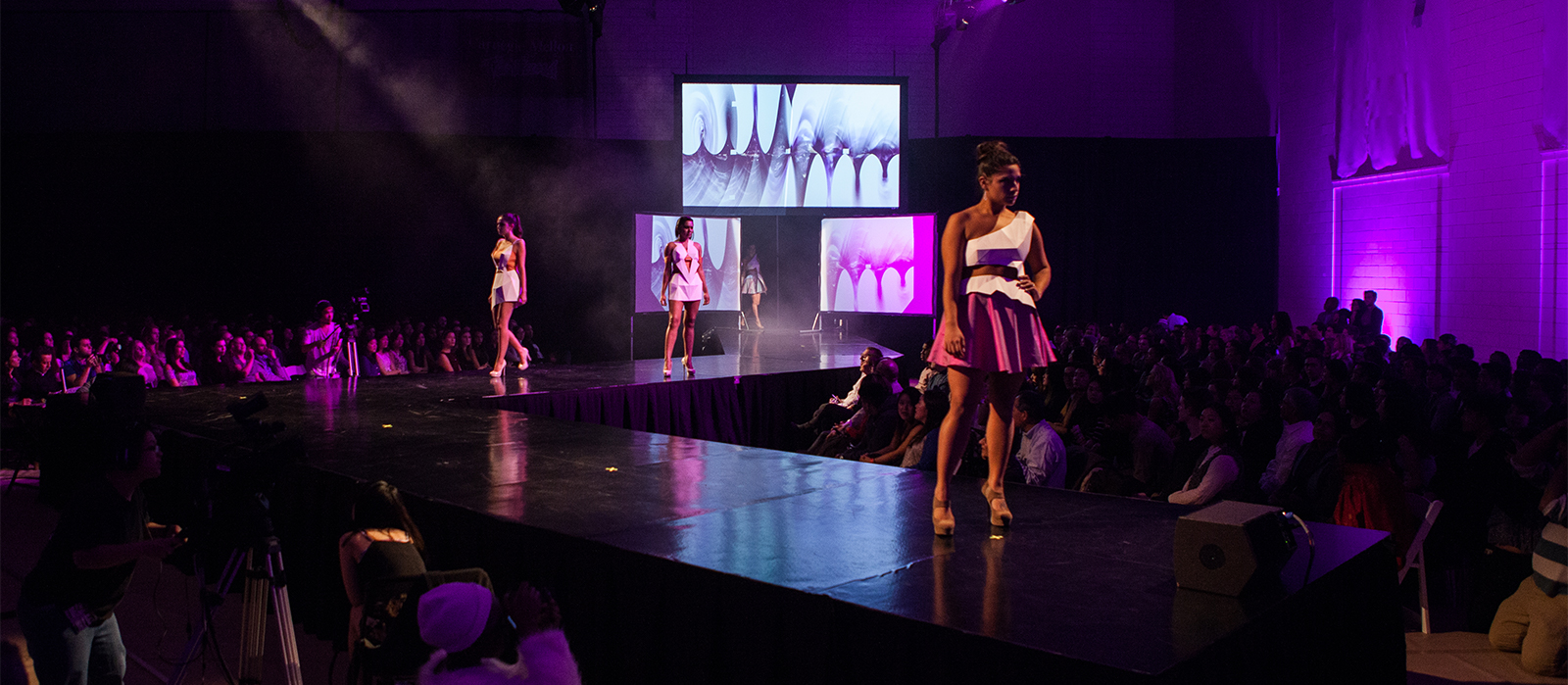
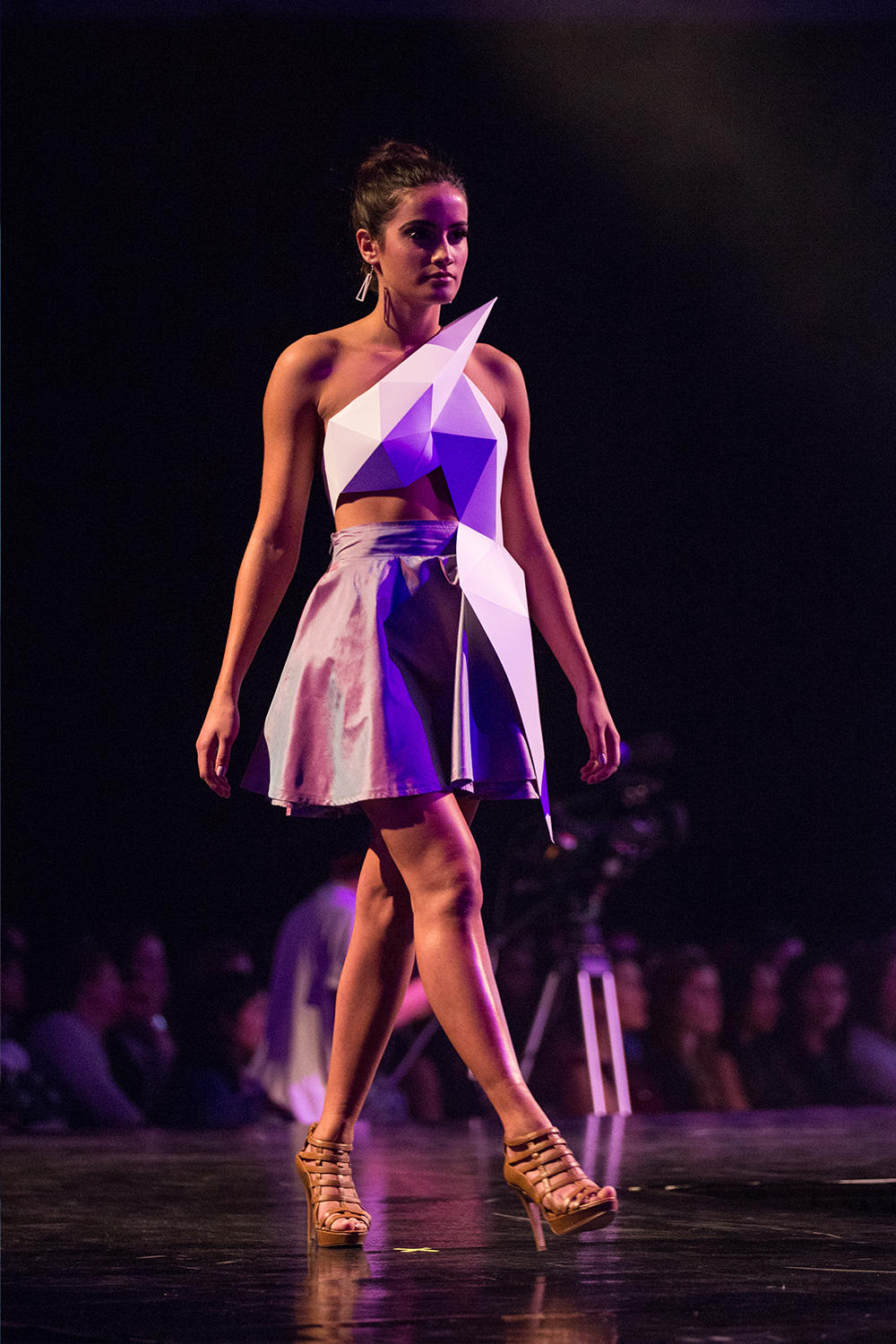
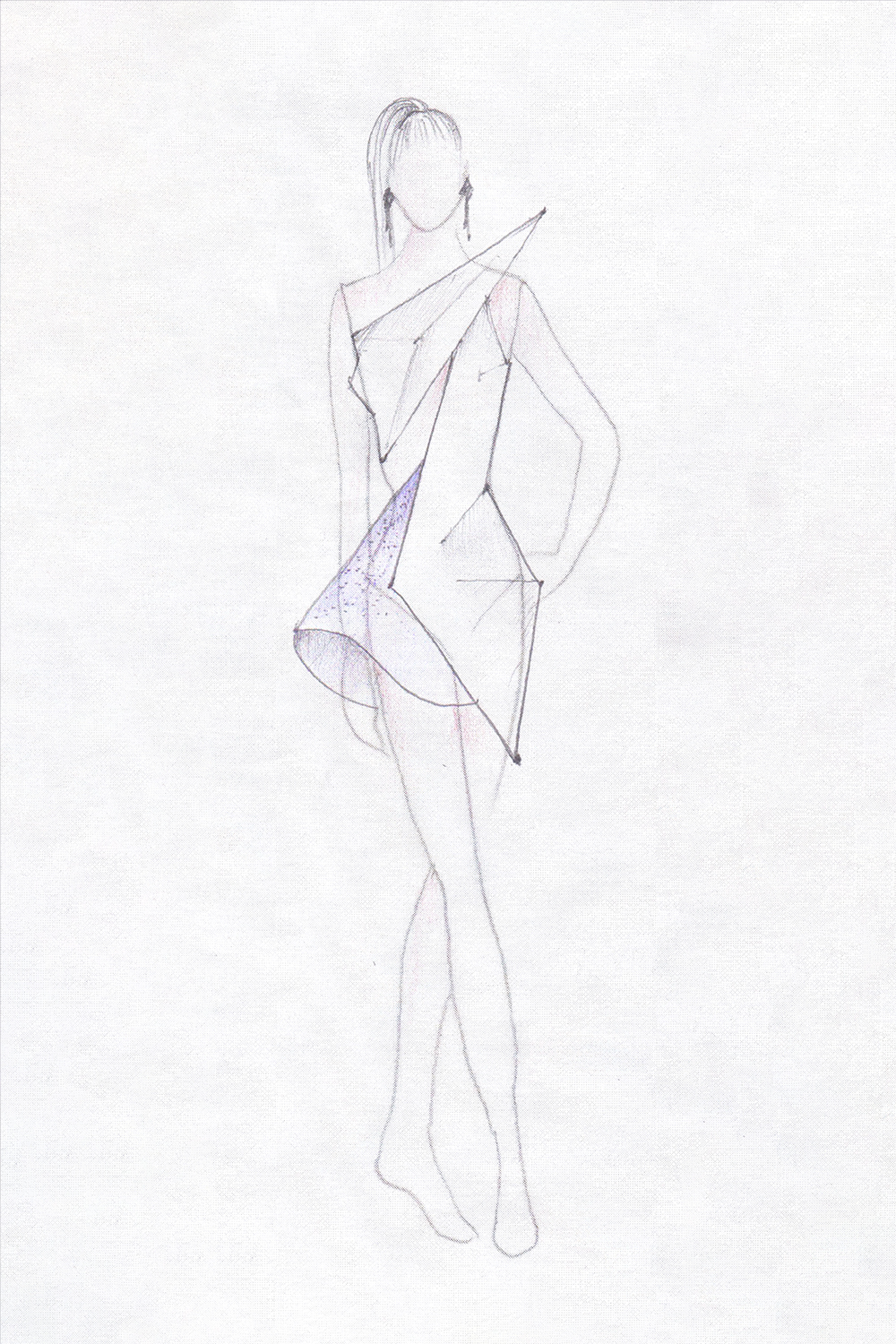
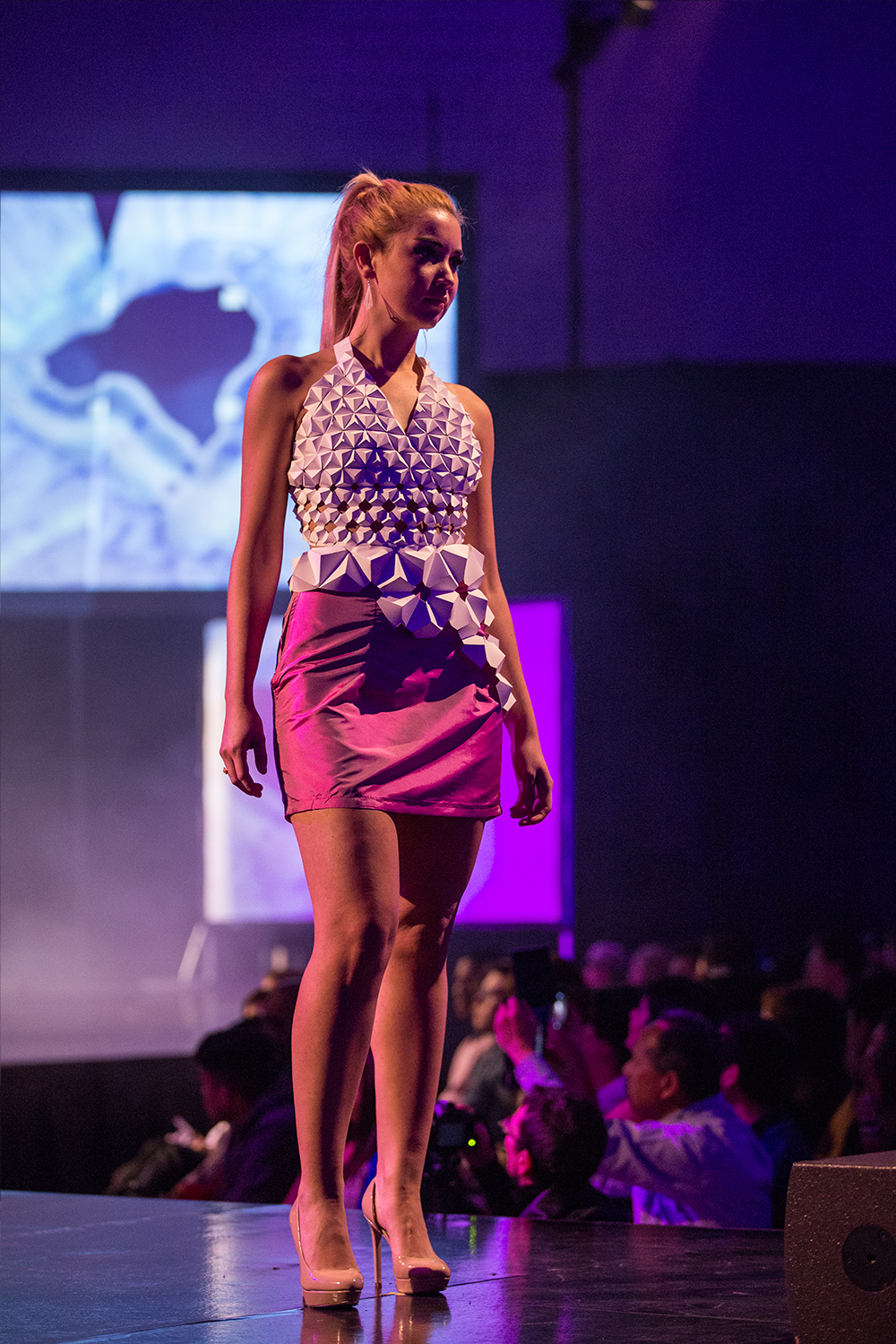
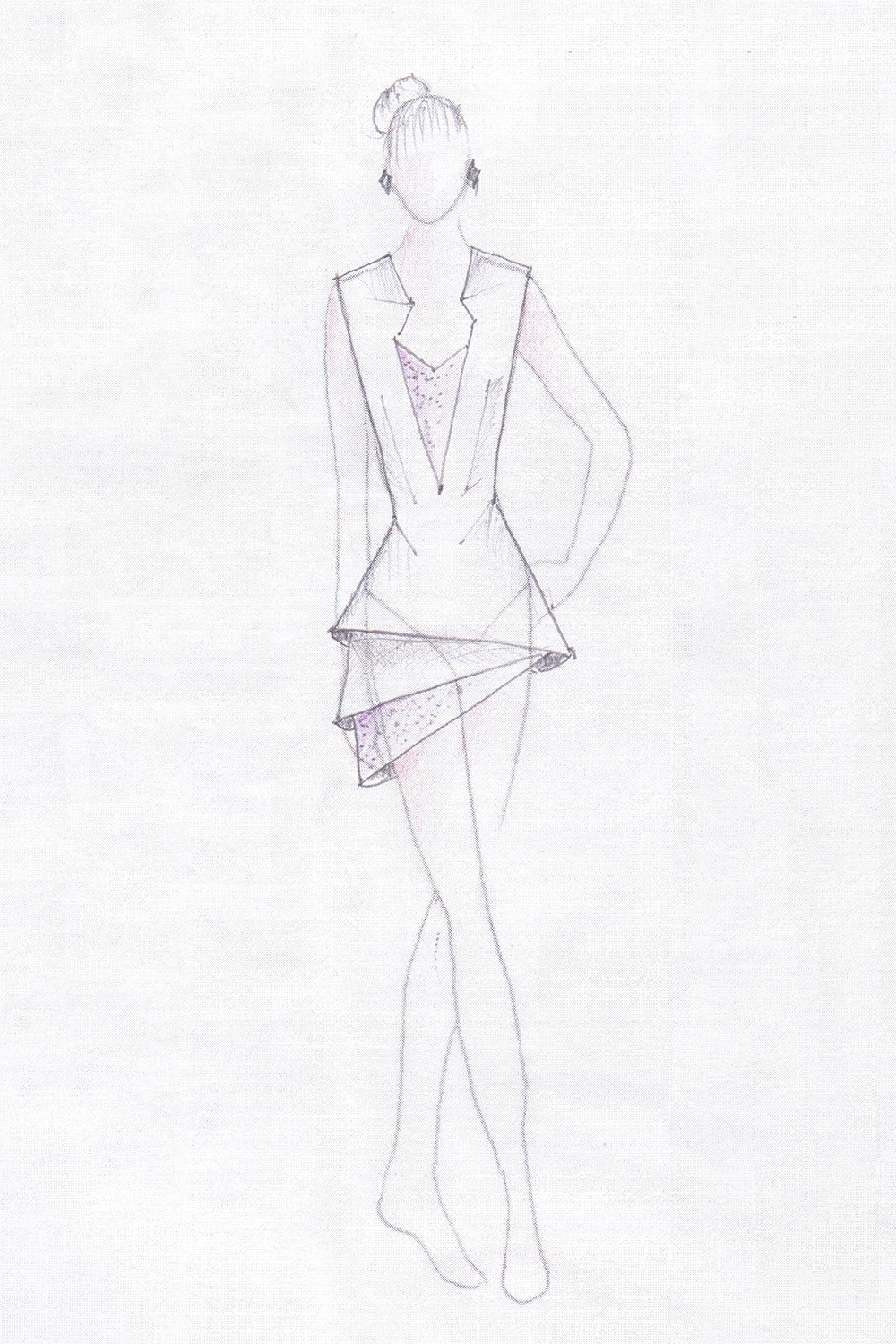
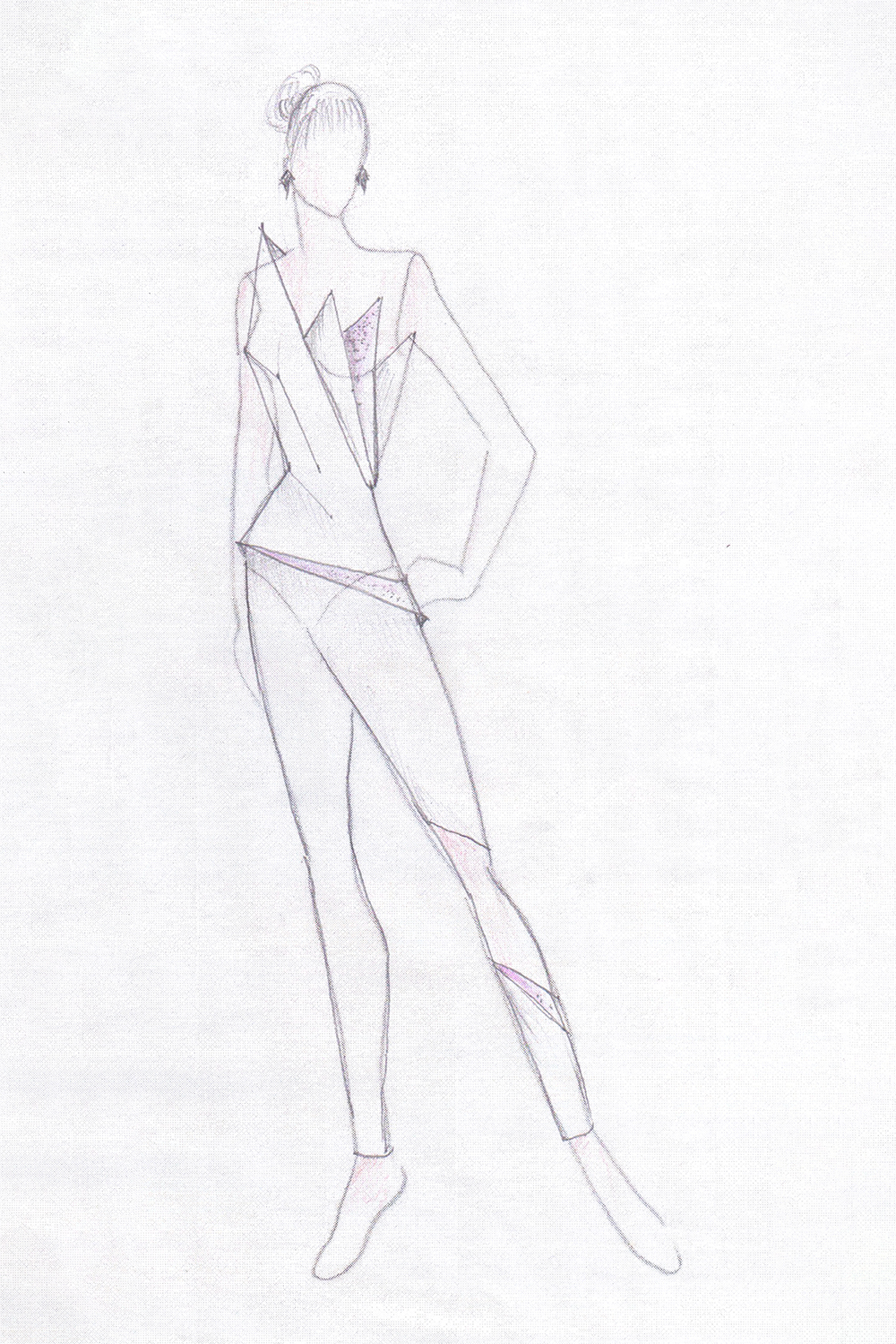
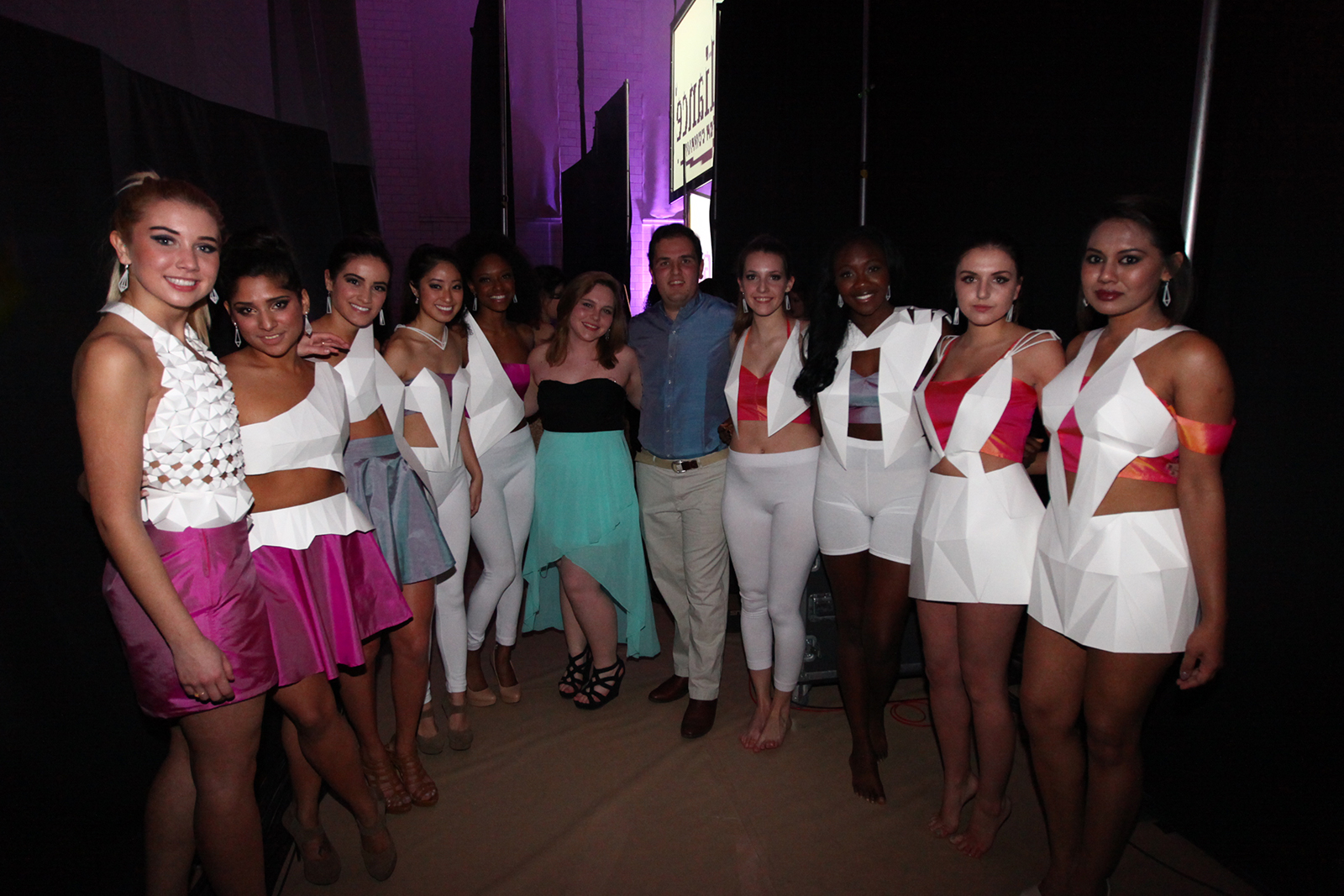
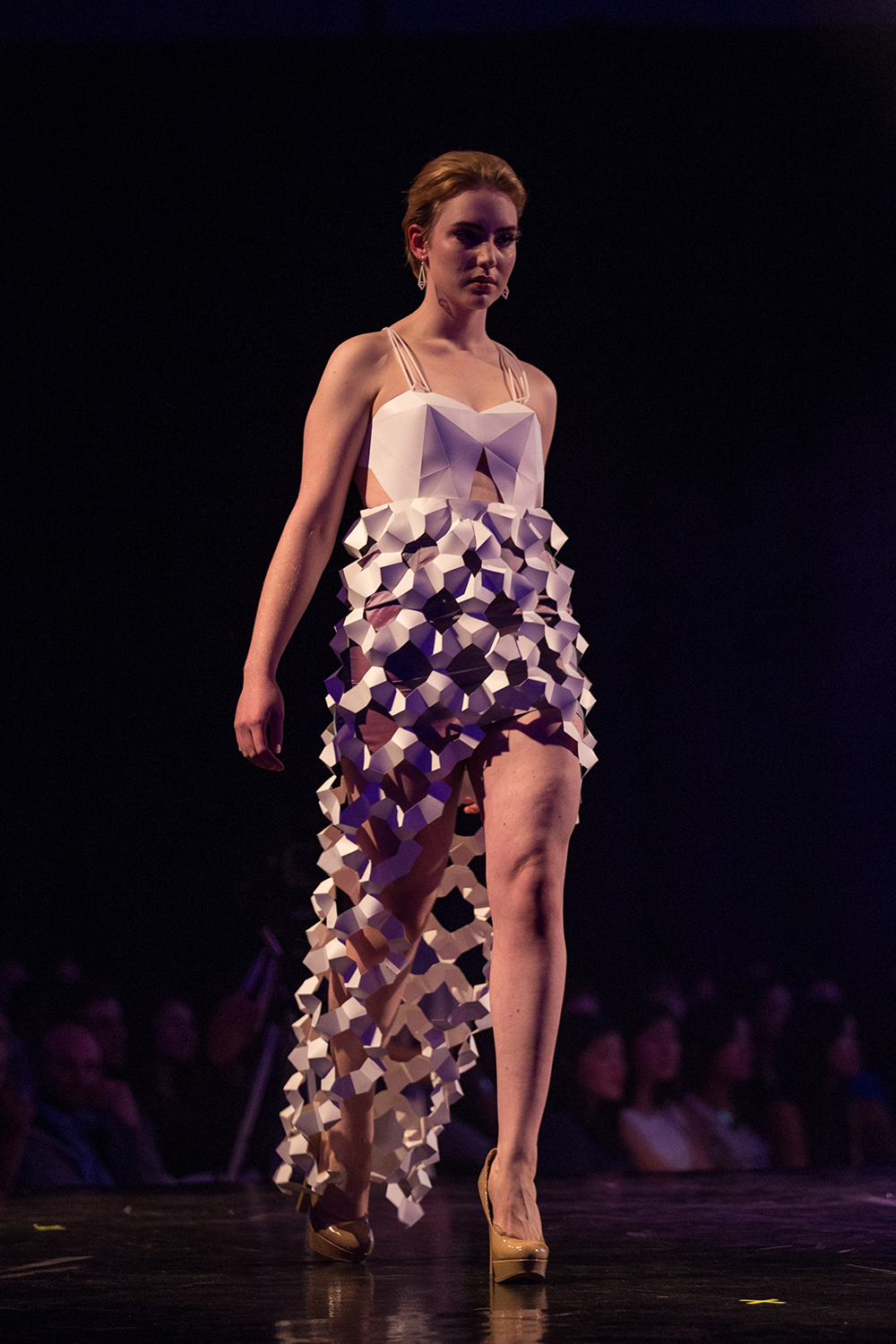
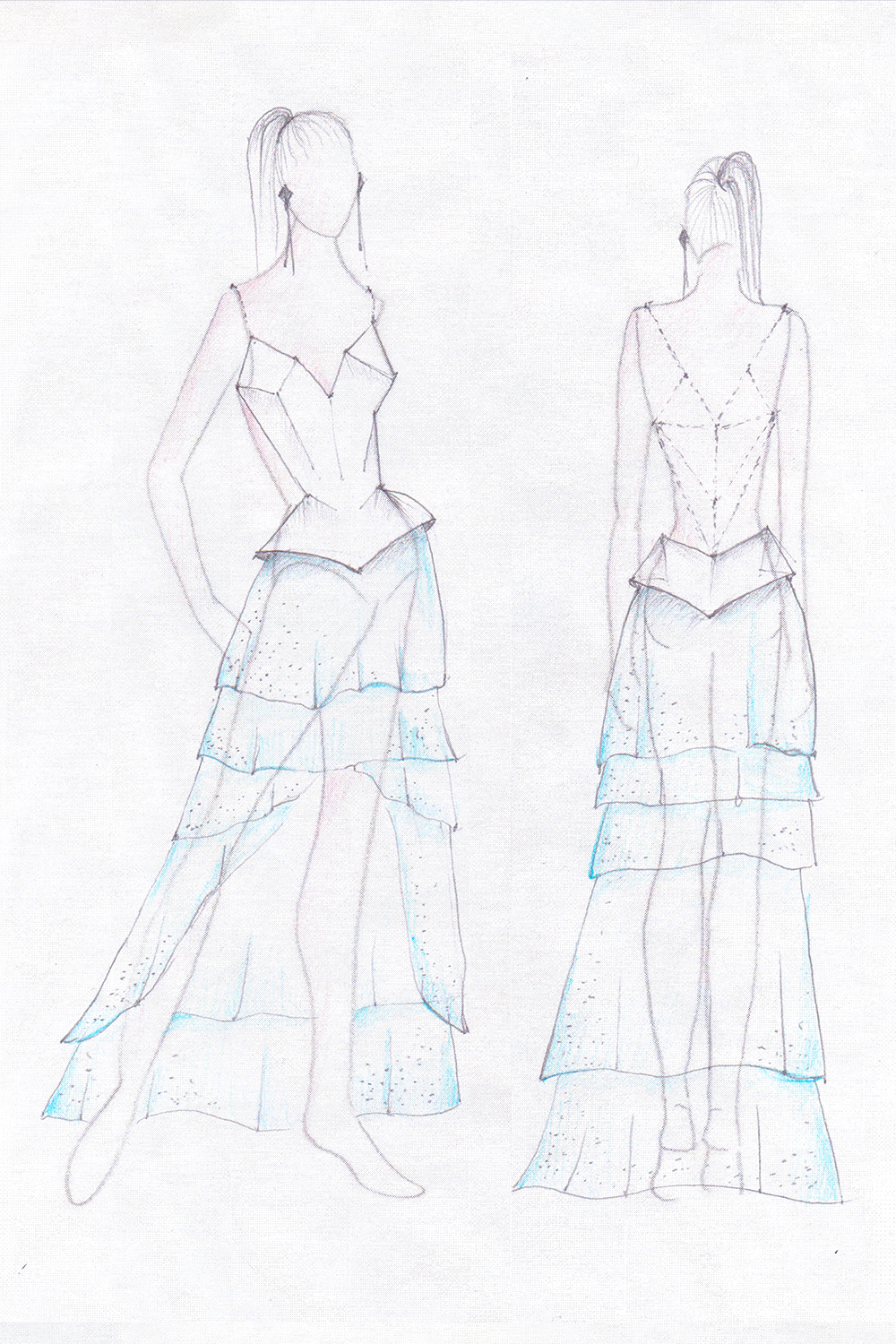
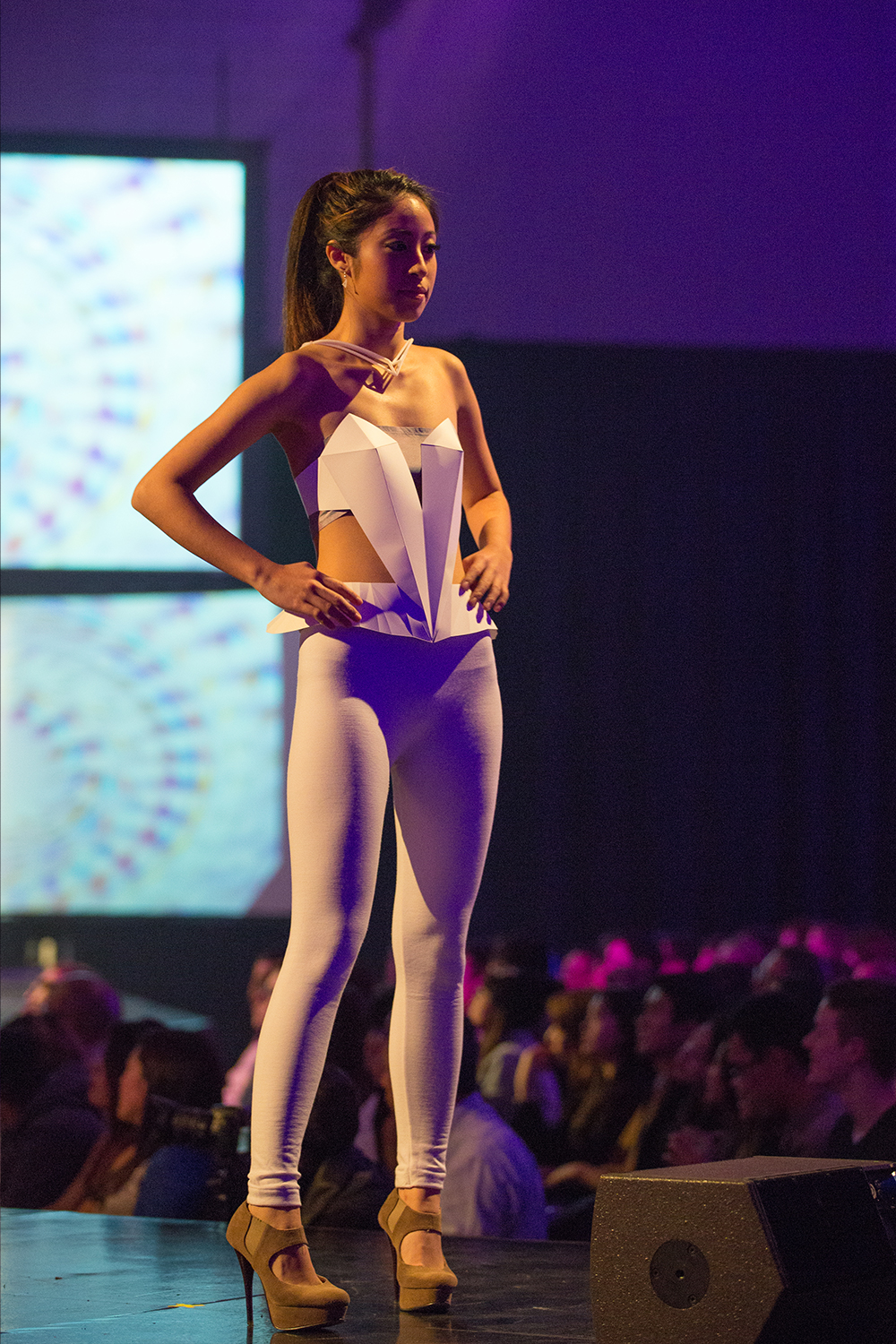
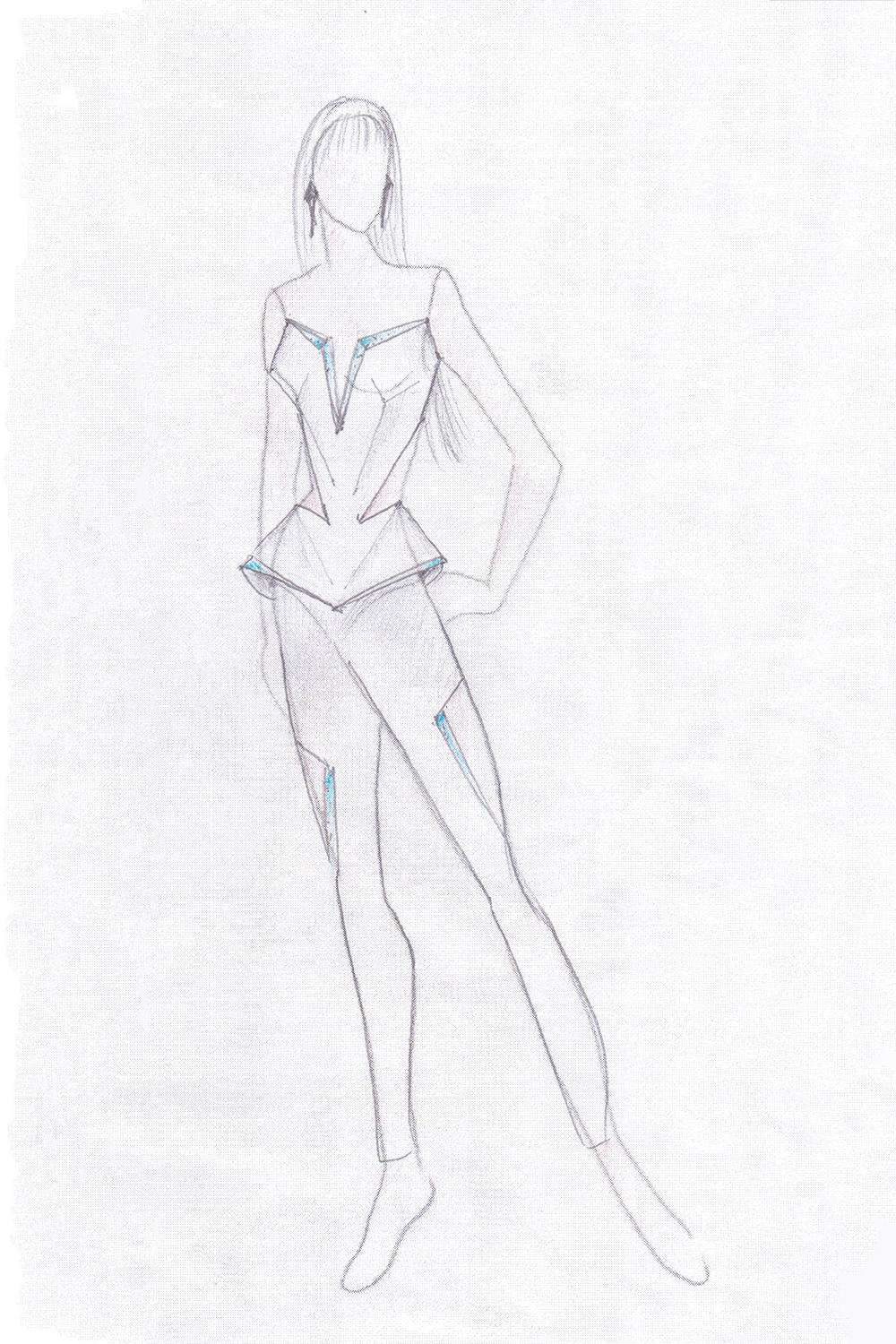

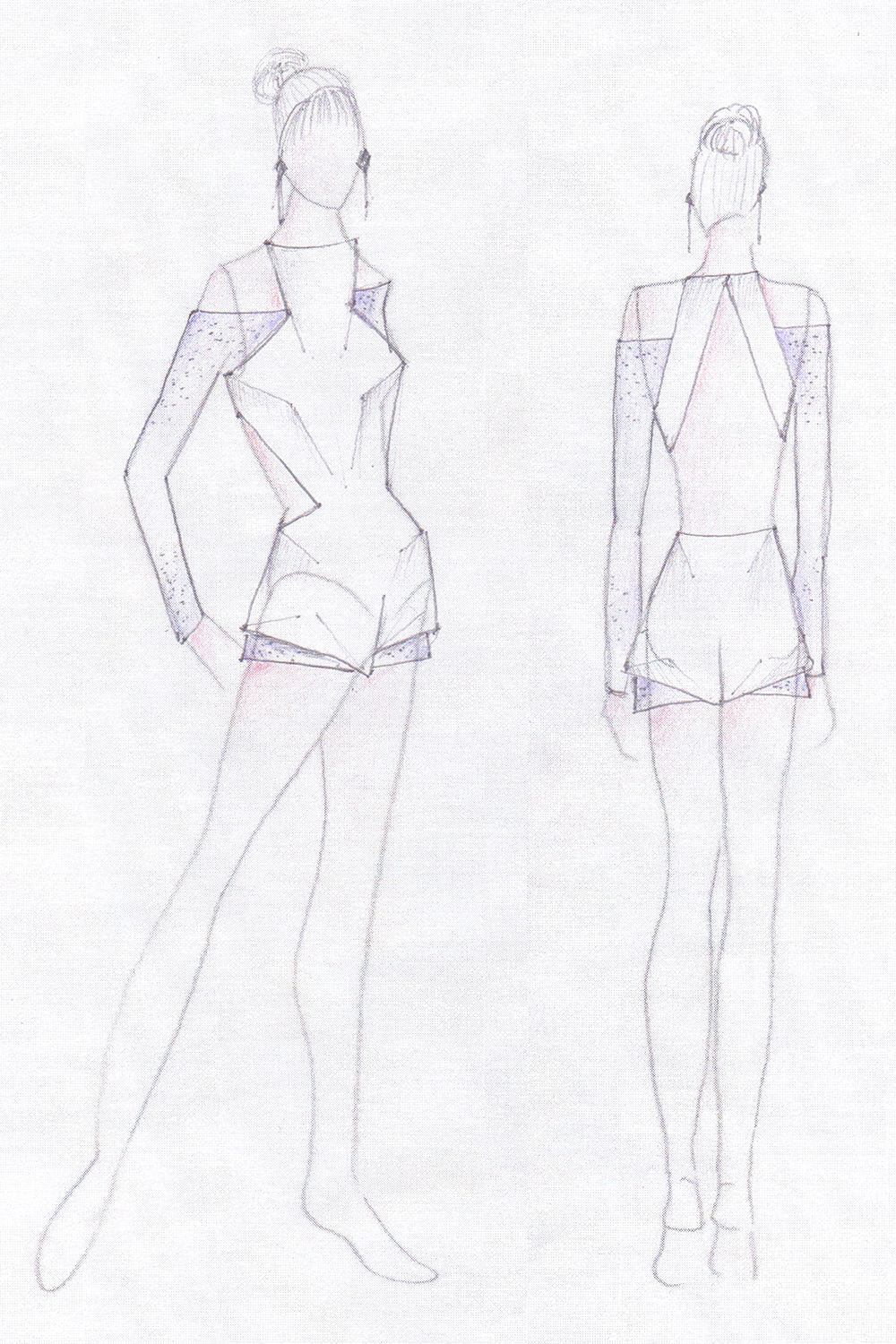
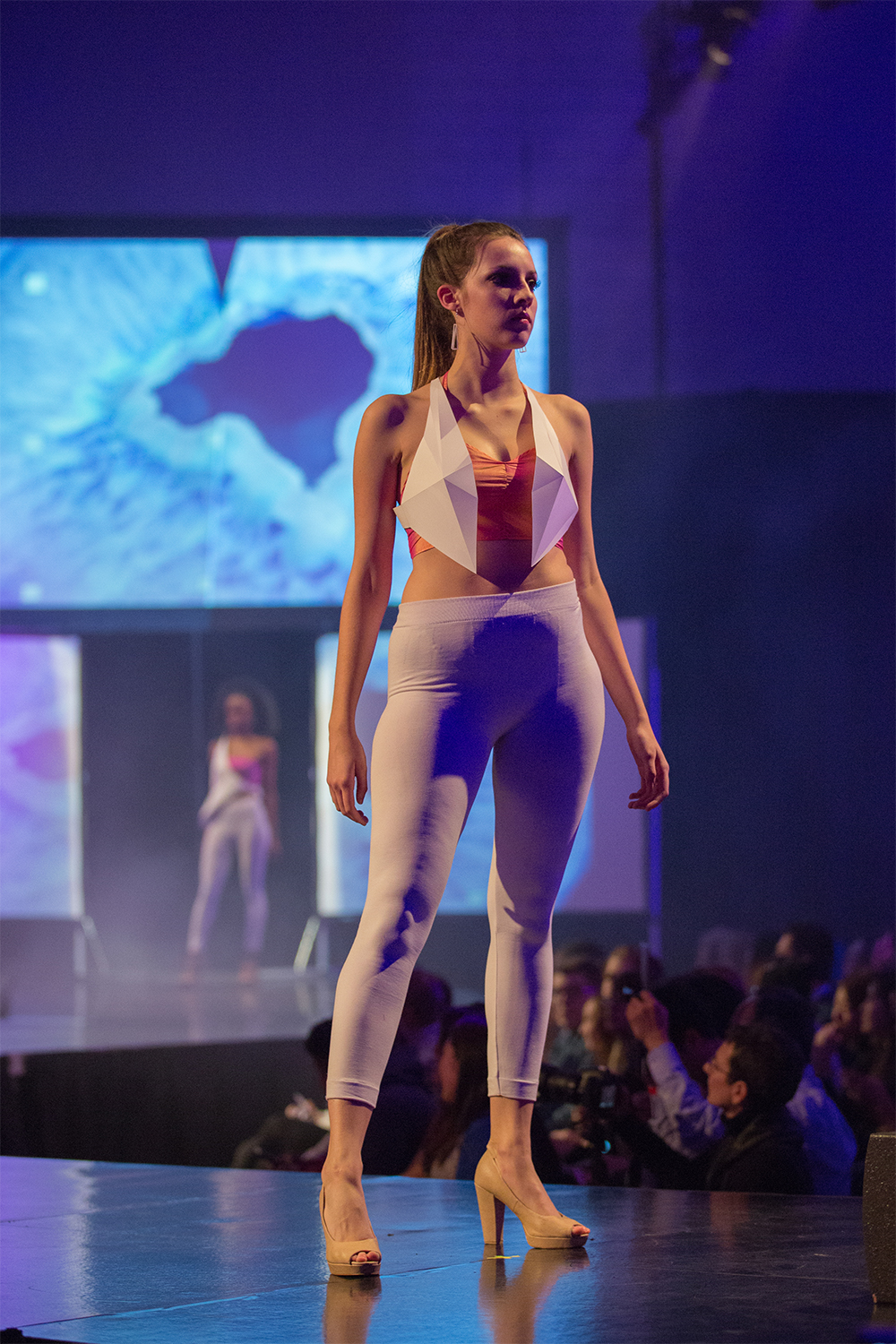
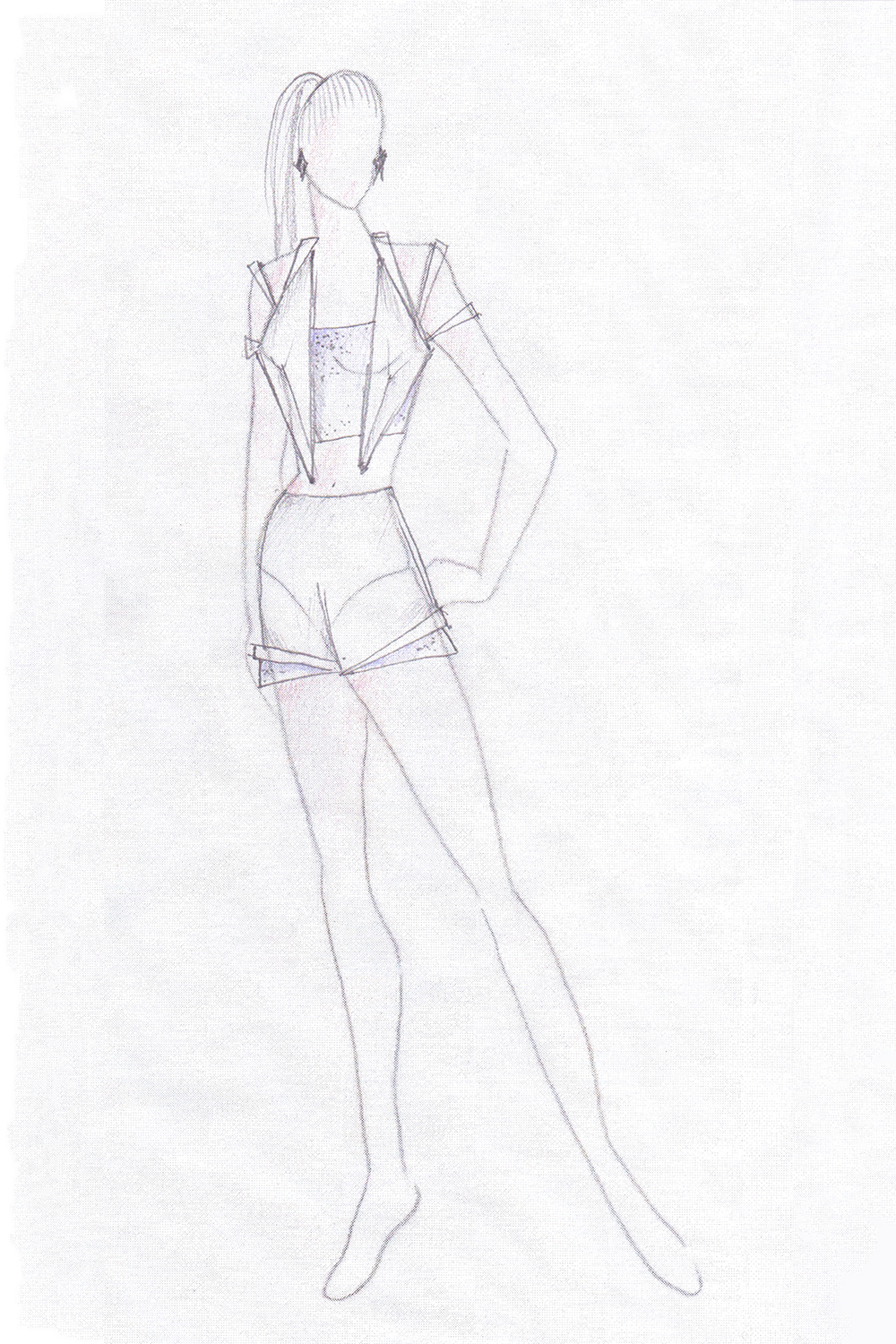
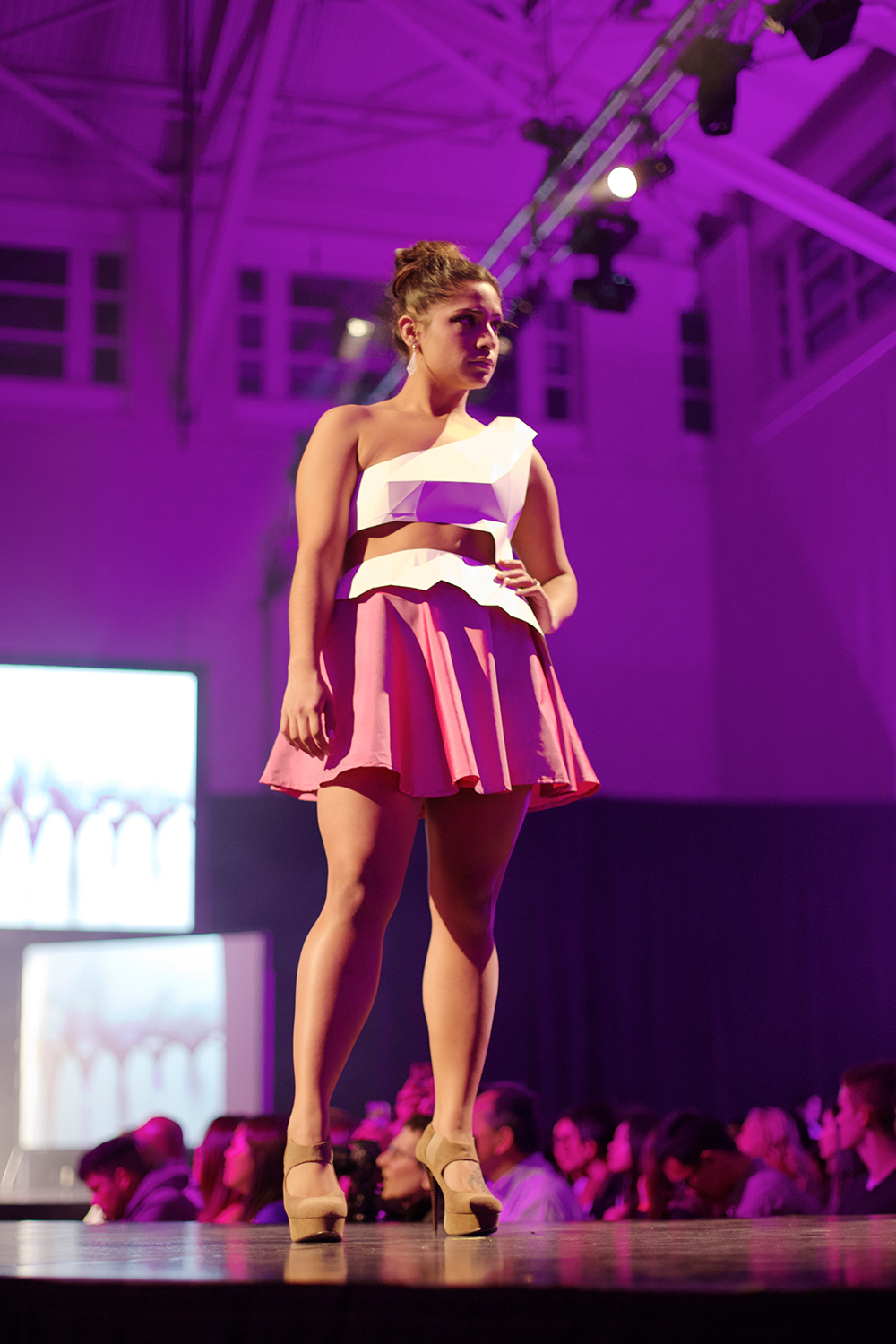
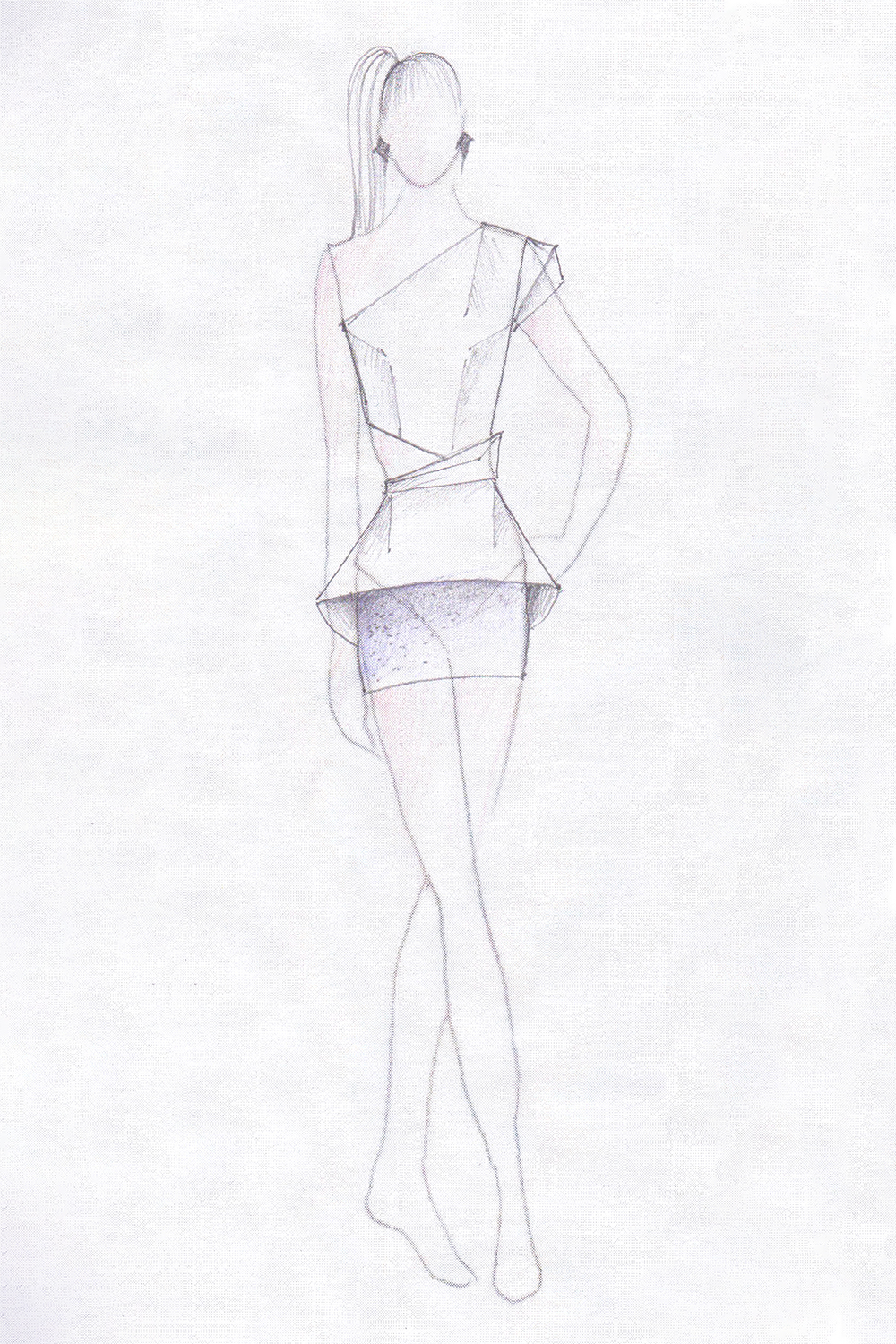
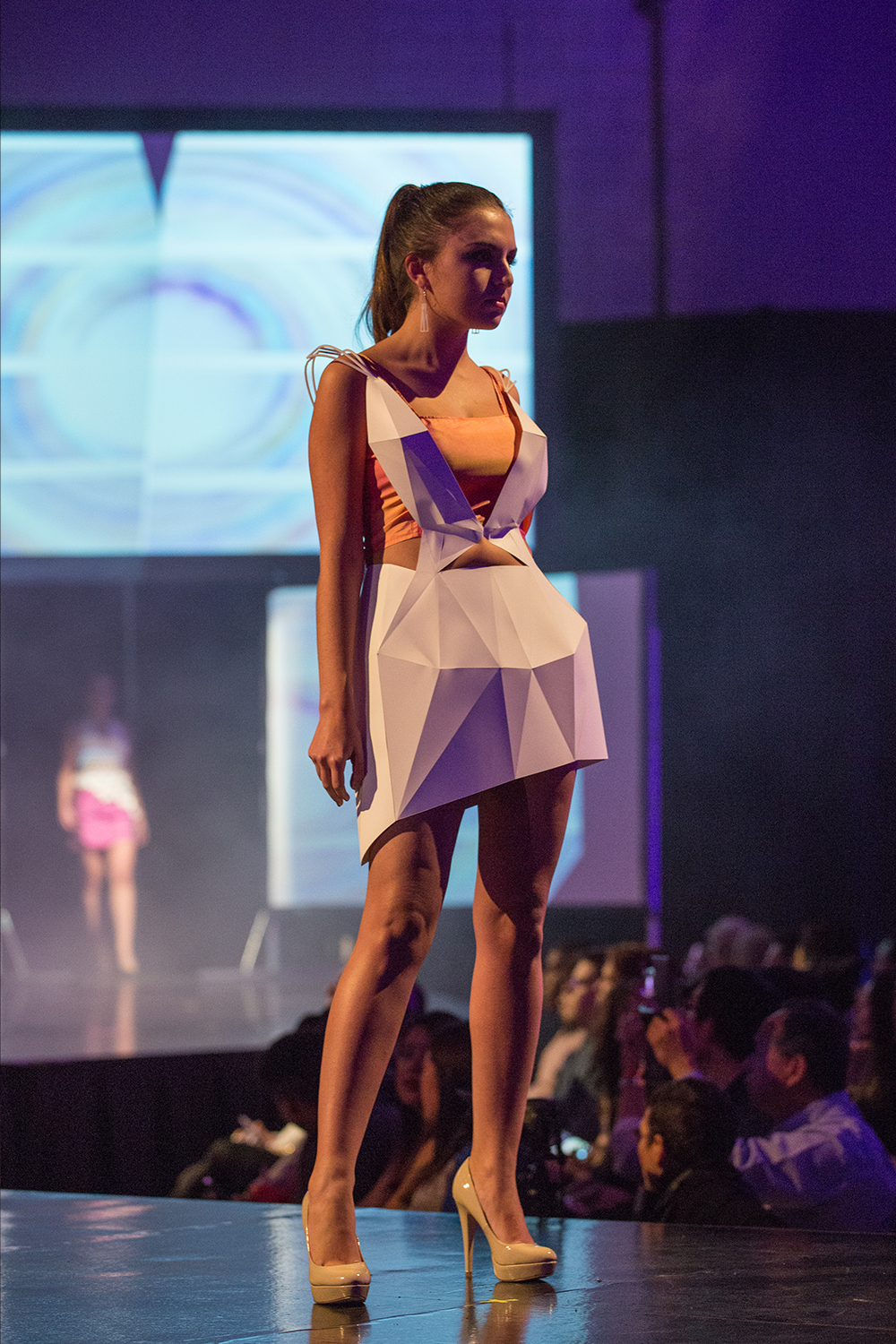
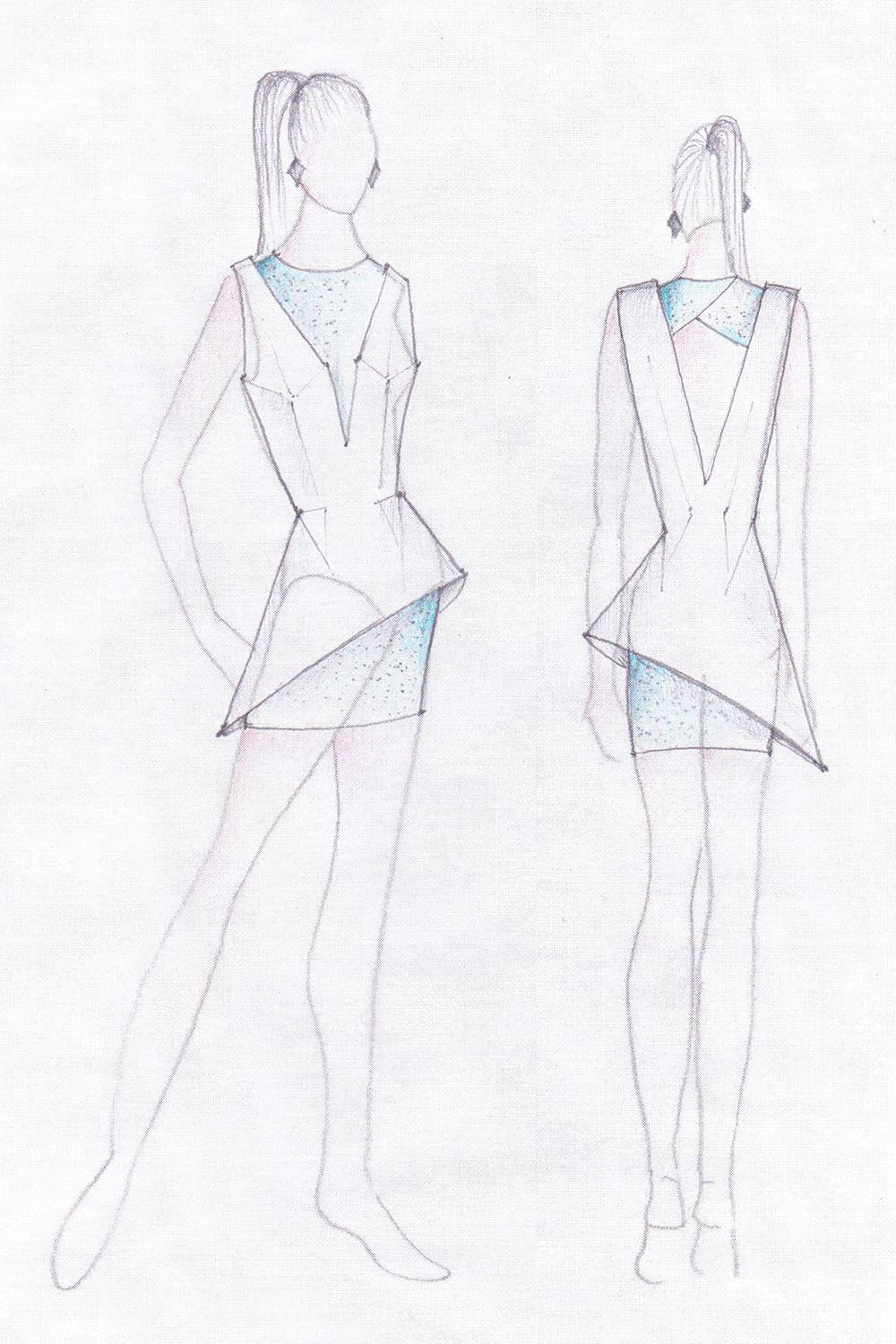
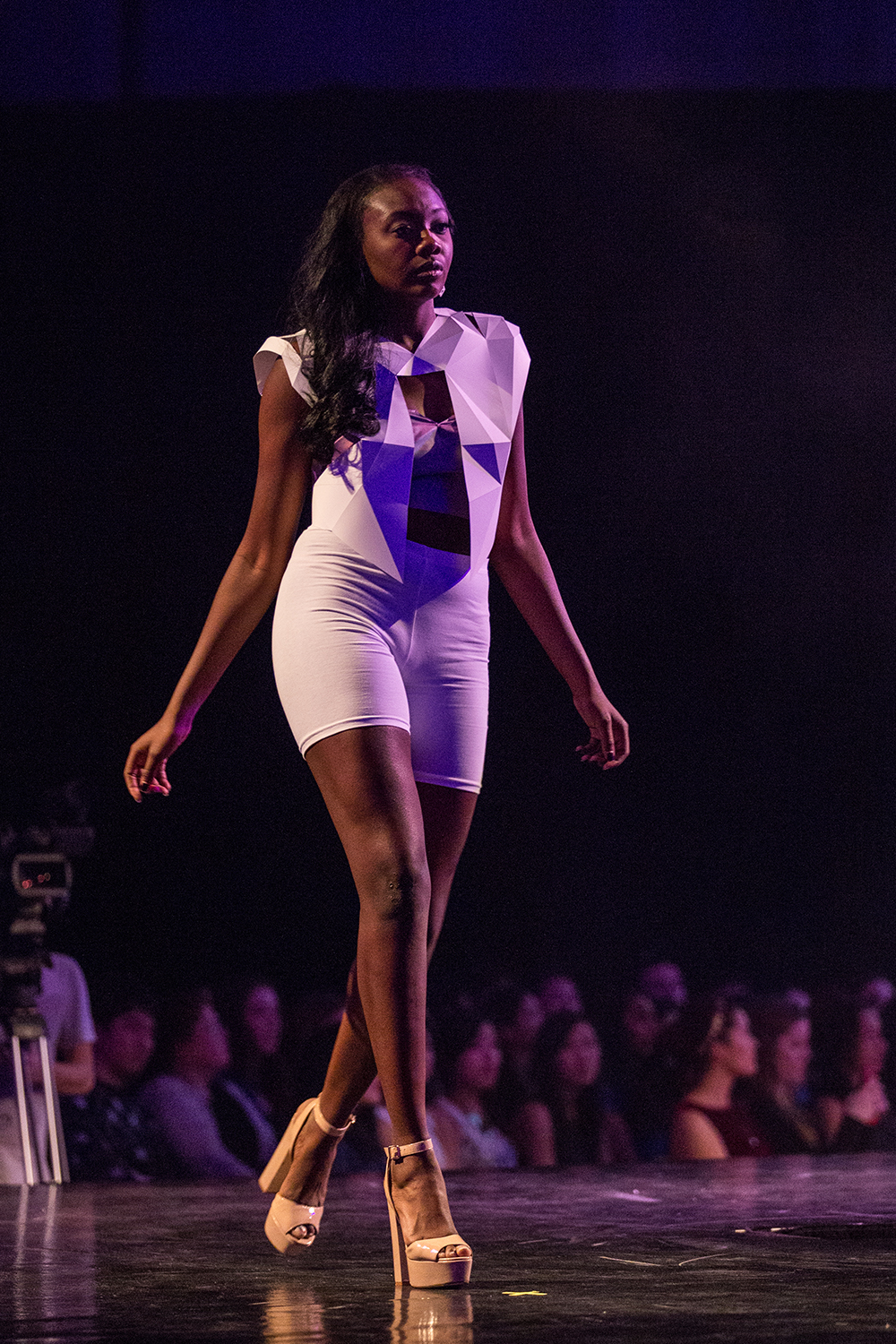
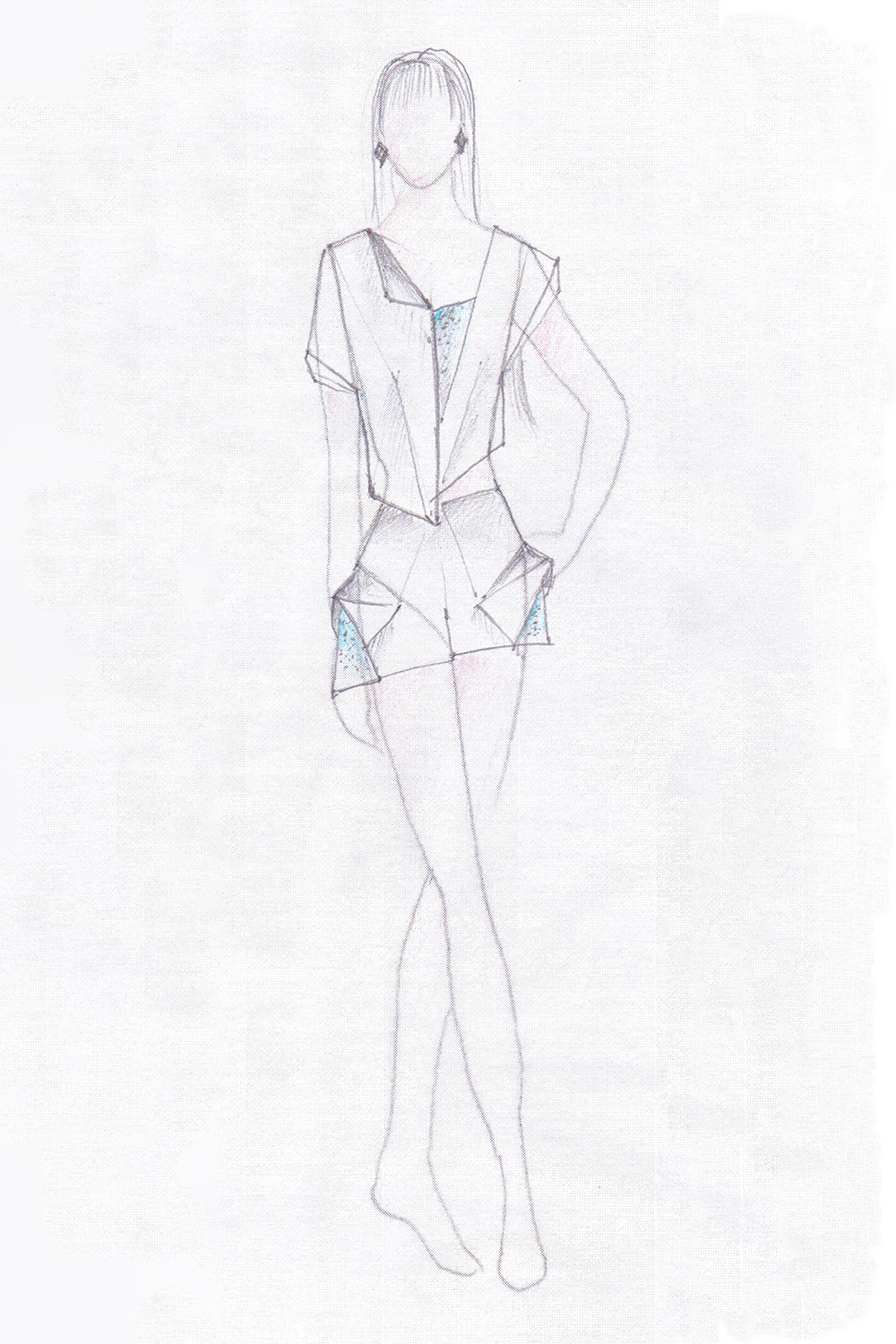
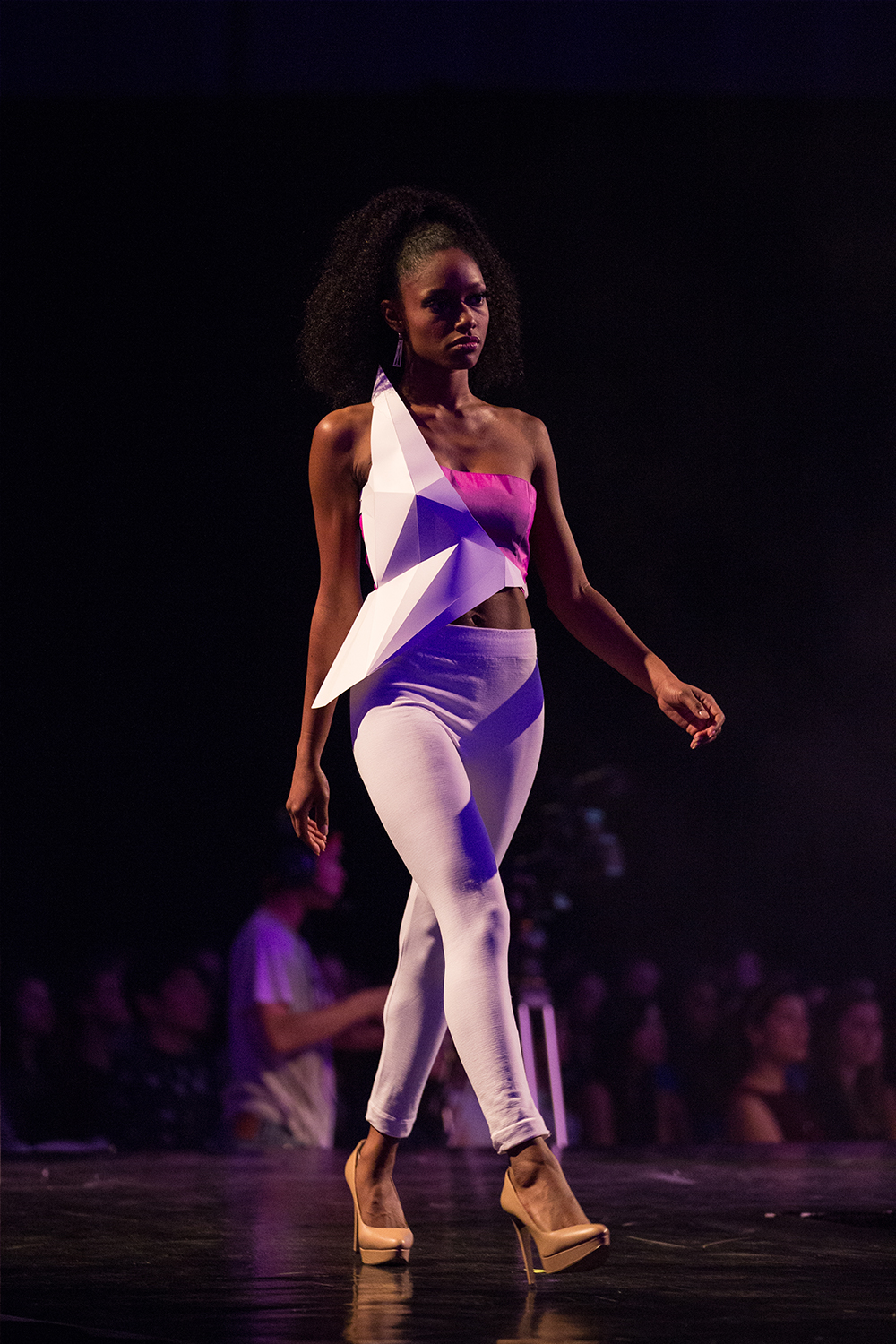
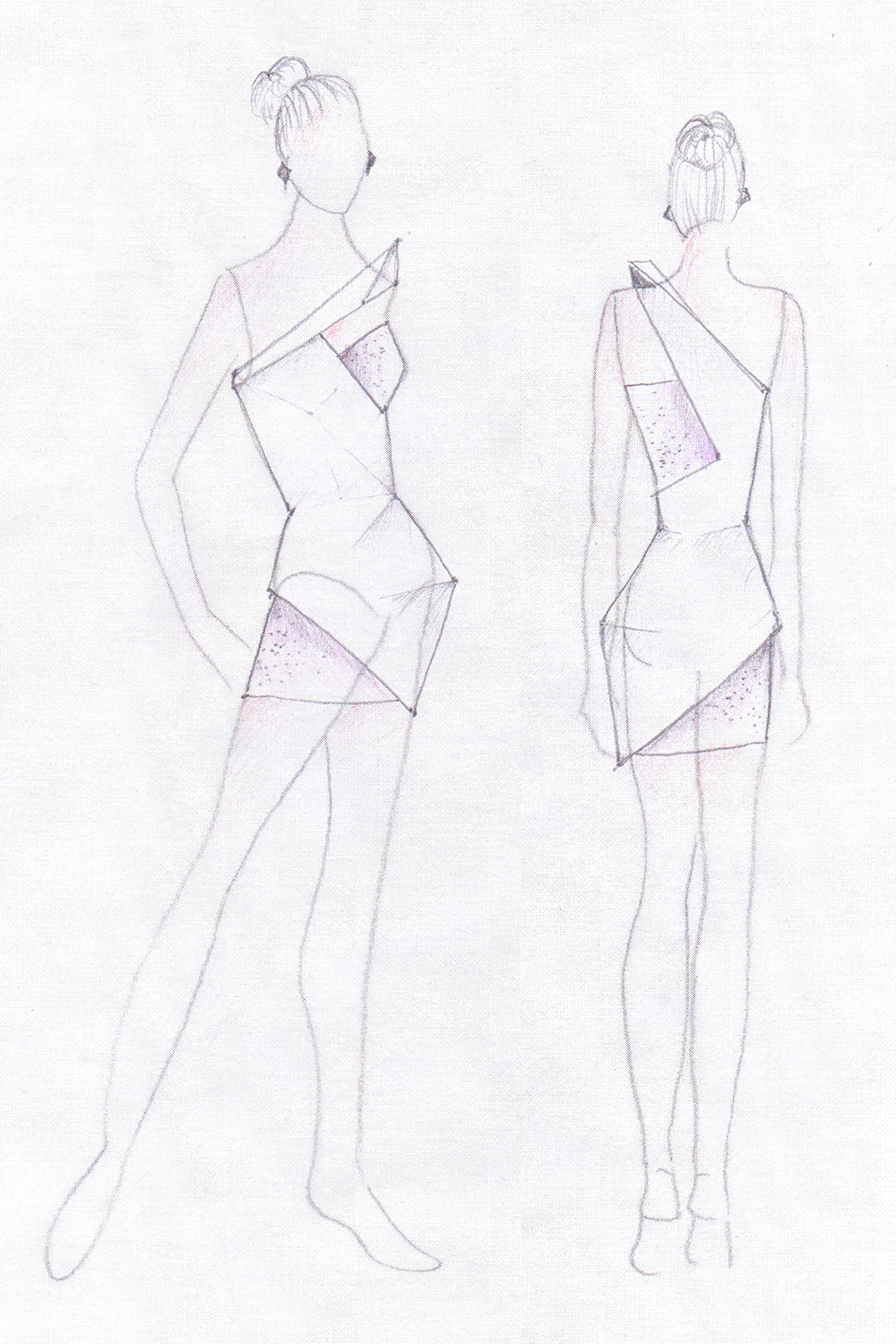
I also want to thank Yupo Opens a new window for being our sponsor for this collection and Jonathan Leung, Yutong Chen and Victor Song for many of the wonderful photos you see.
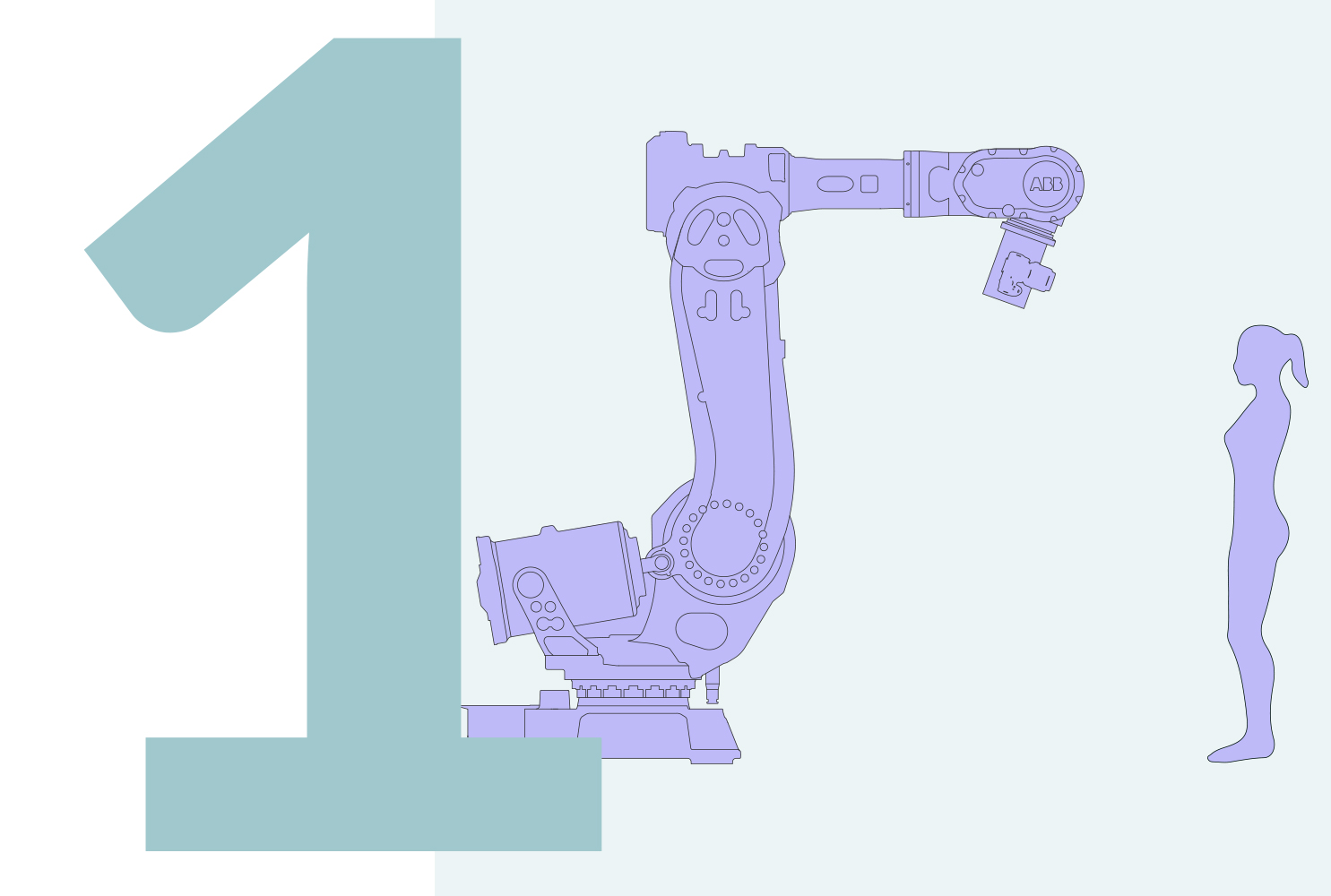
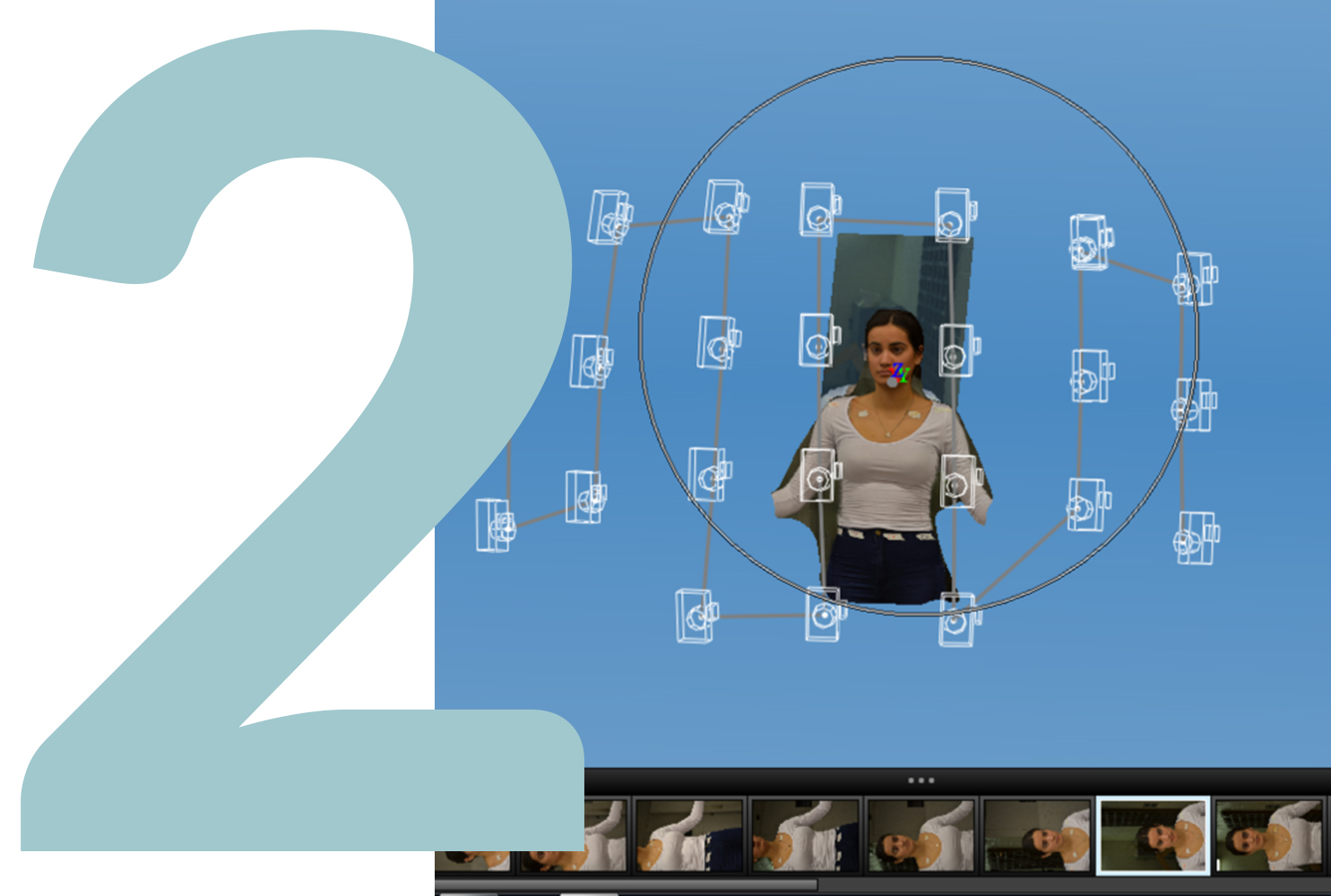
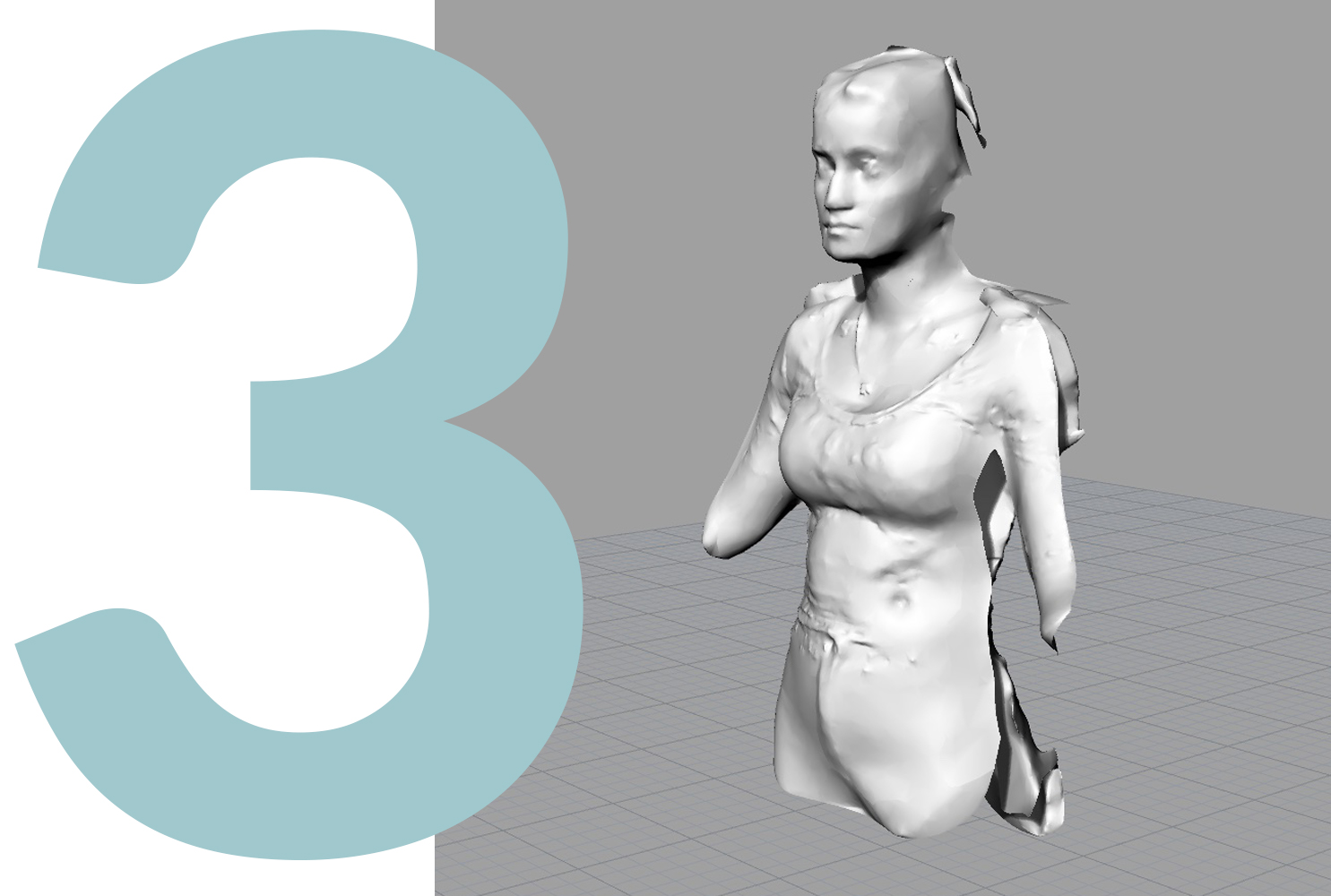
A new take on fashion production
In order to reduce the number of fitting we had to do with the models and experiment with unconventional ways to create a fashion line we decided to 3D scan our models.
We did this by using a ABB robot (those big robotic arms you generally see assembling cars), with a camera mounted to it taking several dozen photos of our models then converted those images into digital 3D models, using photogrammetry techniques which we could then fit and design our looks around.
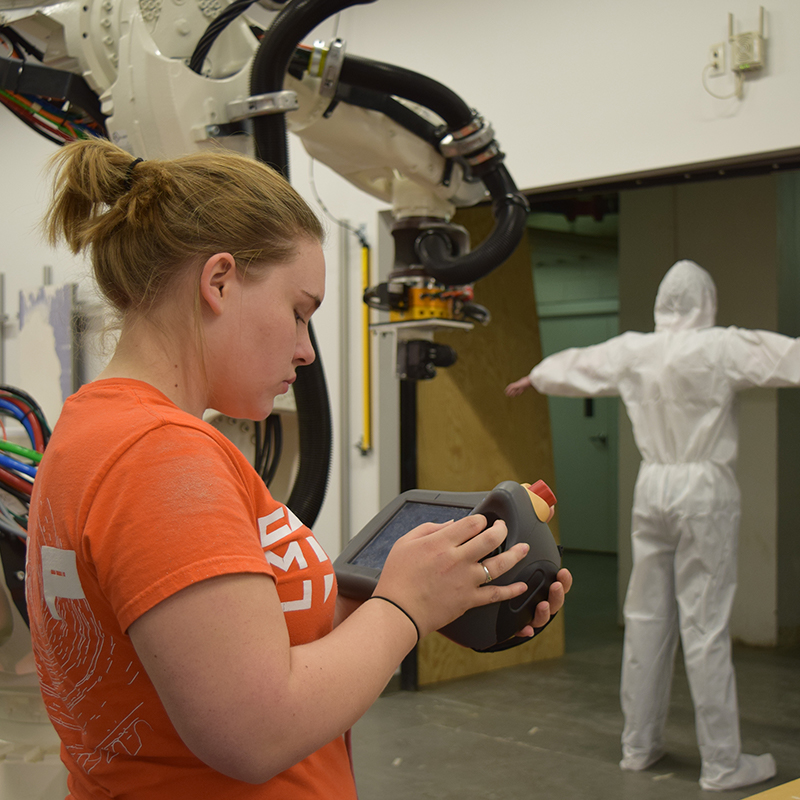
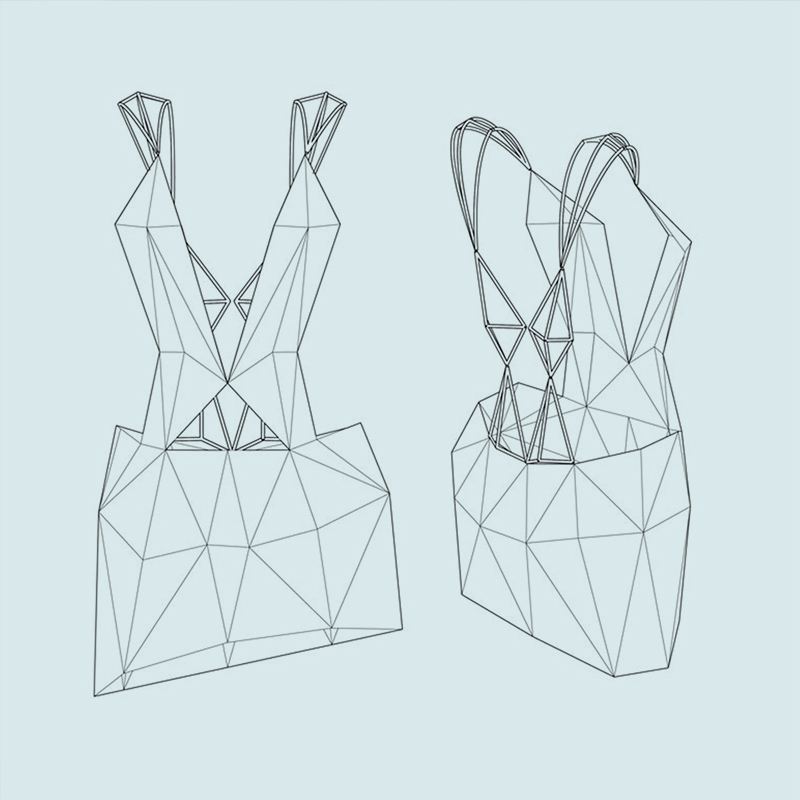
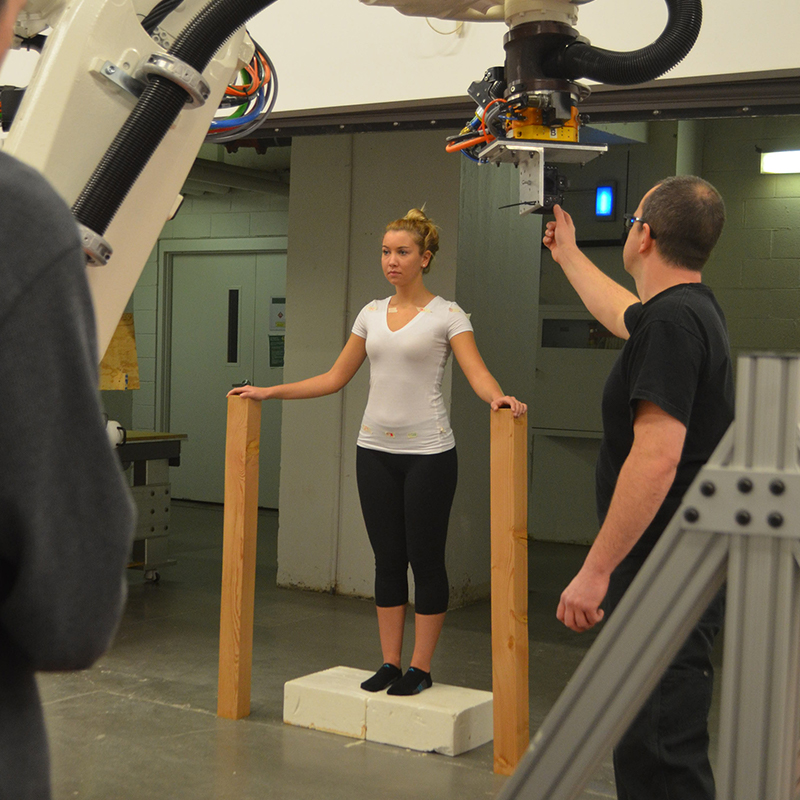
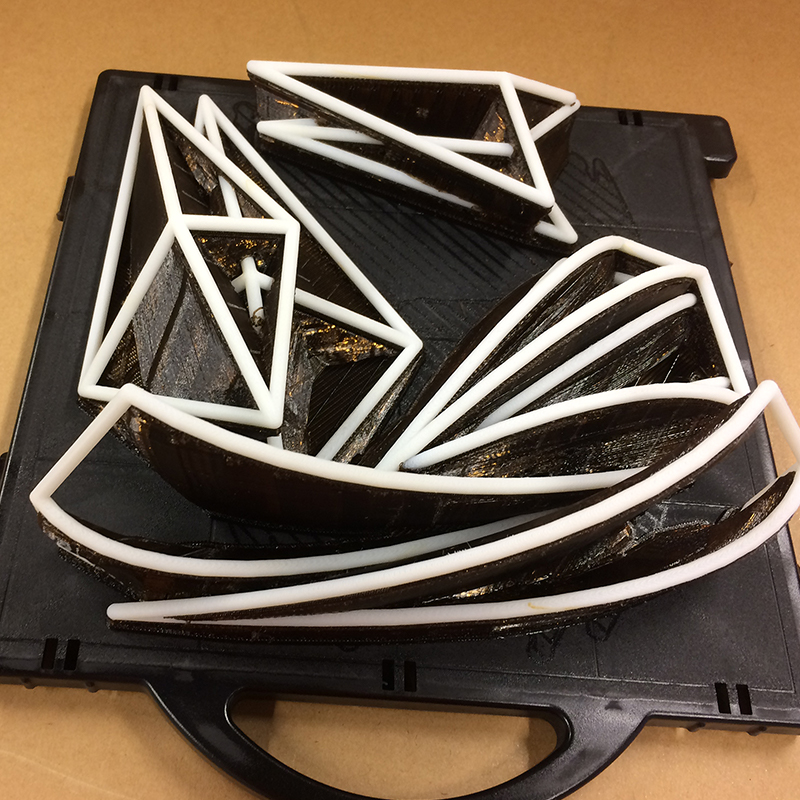
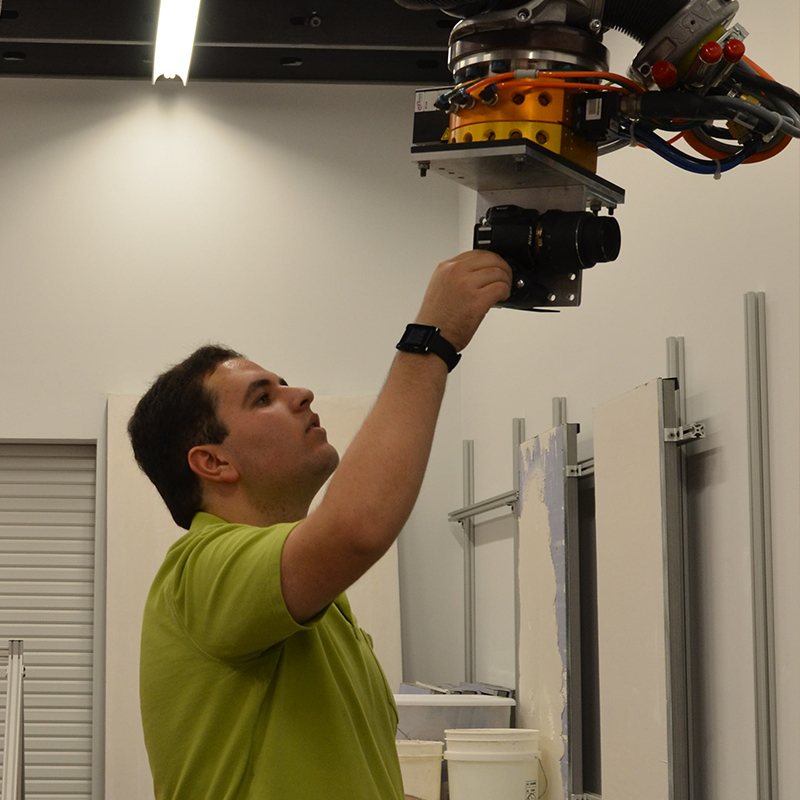
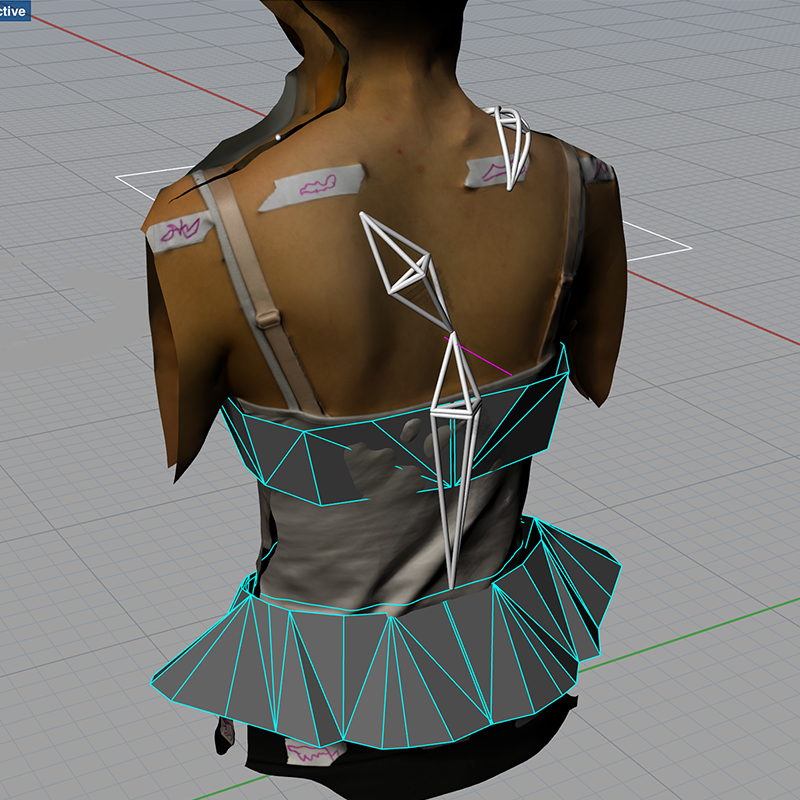

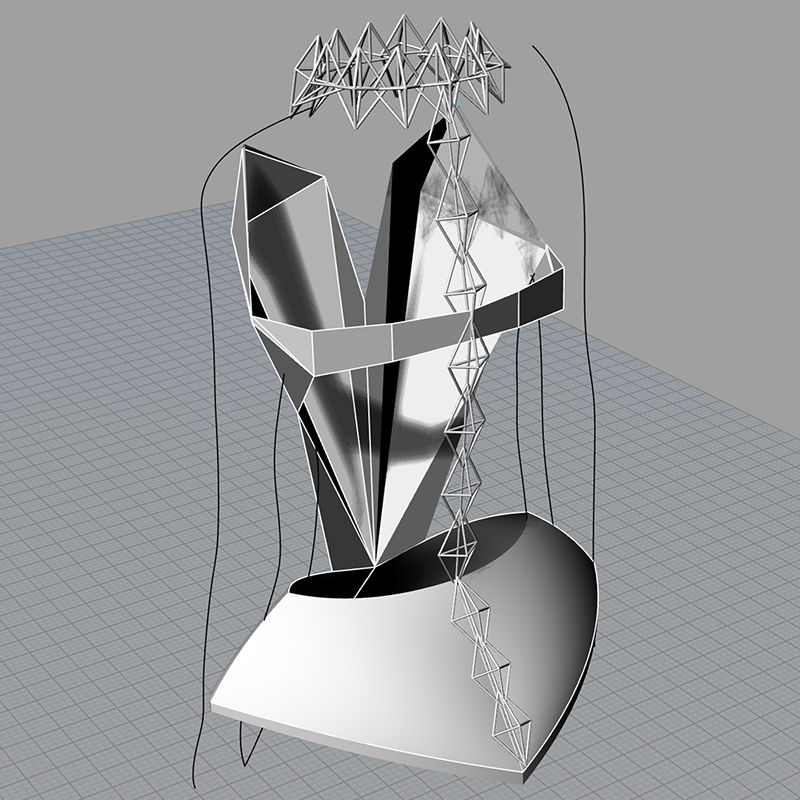
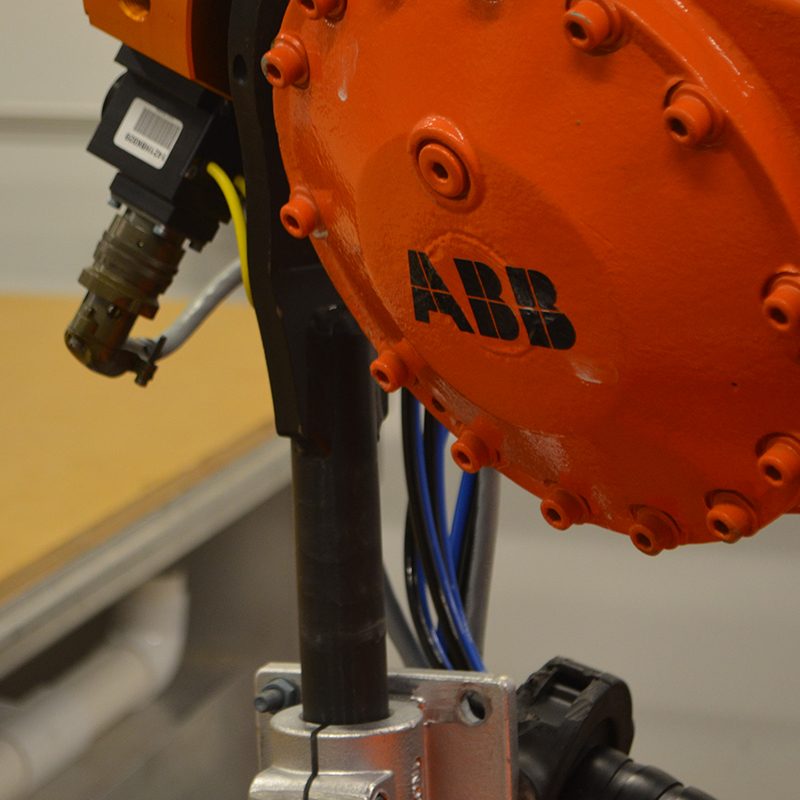
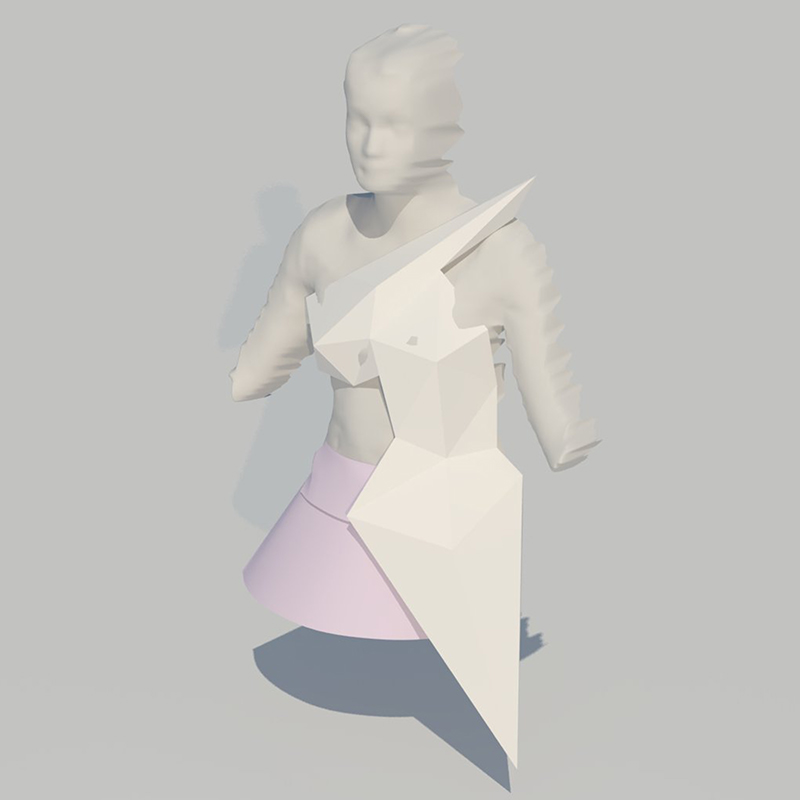
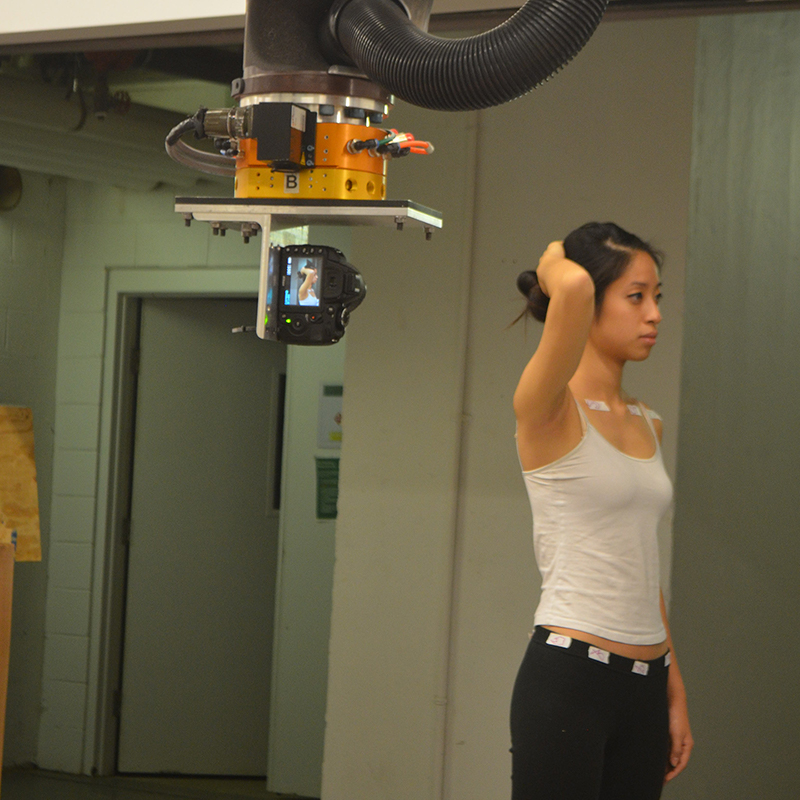
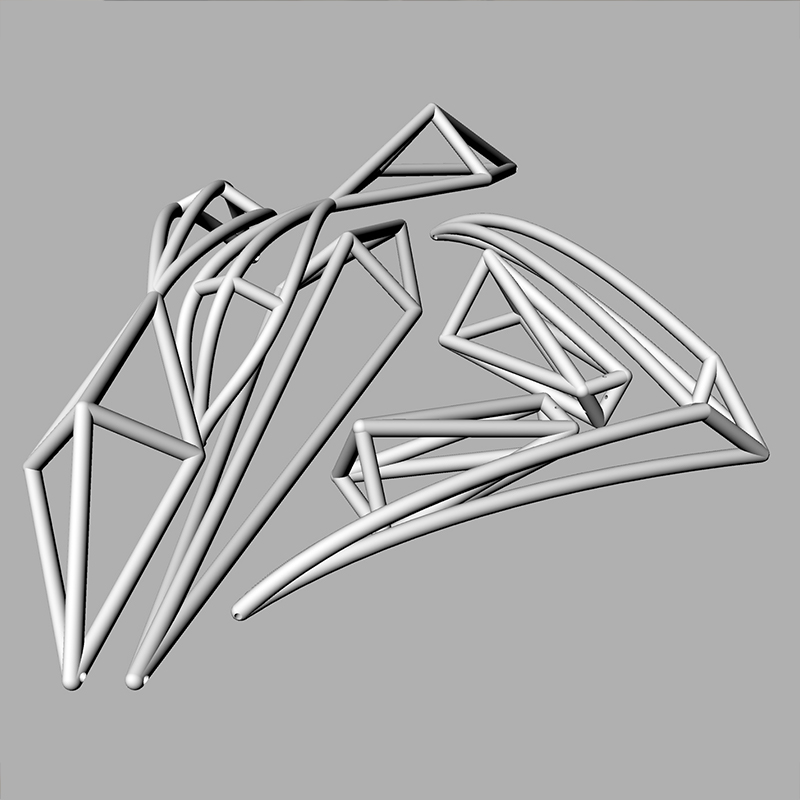
Behind the Scenes
This project took quite a bit of computing power often times more them we had available. We regularly crashed several of our design tools as we tried to created higher resolutions pieces and while increasing the number of automated steps.
Lots of iteration as we pushed the tolerances of our tools, from the fidelity of our 3D mesh models to the resolution of our 3D prints.
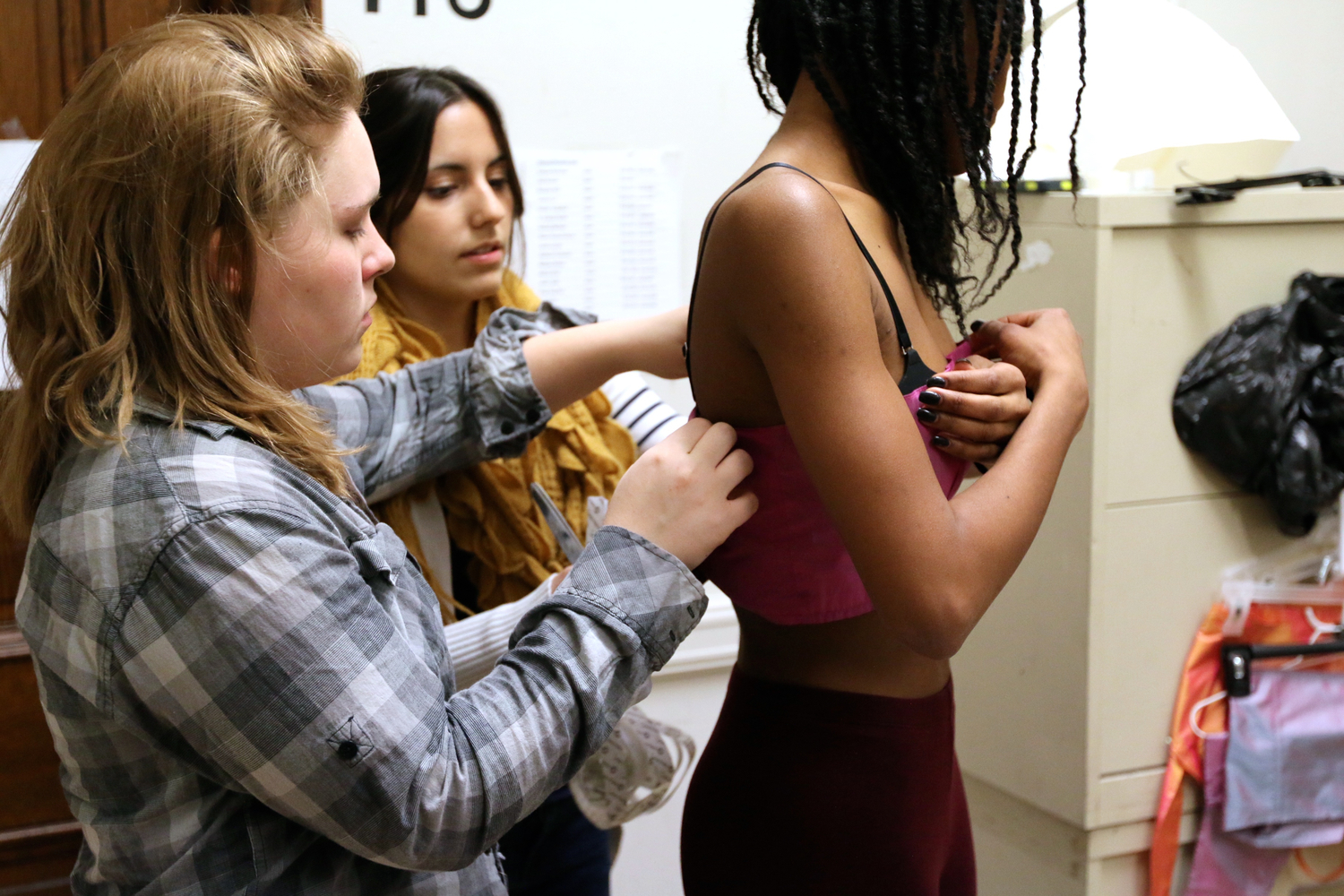
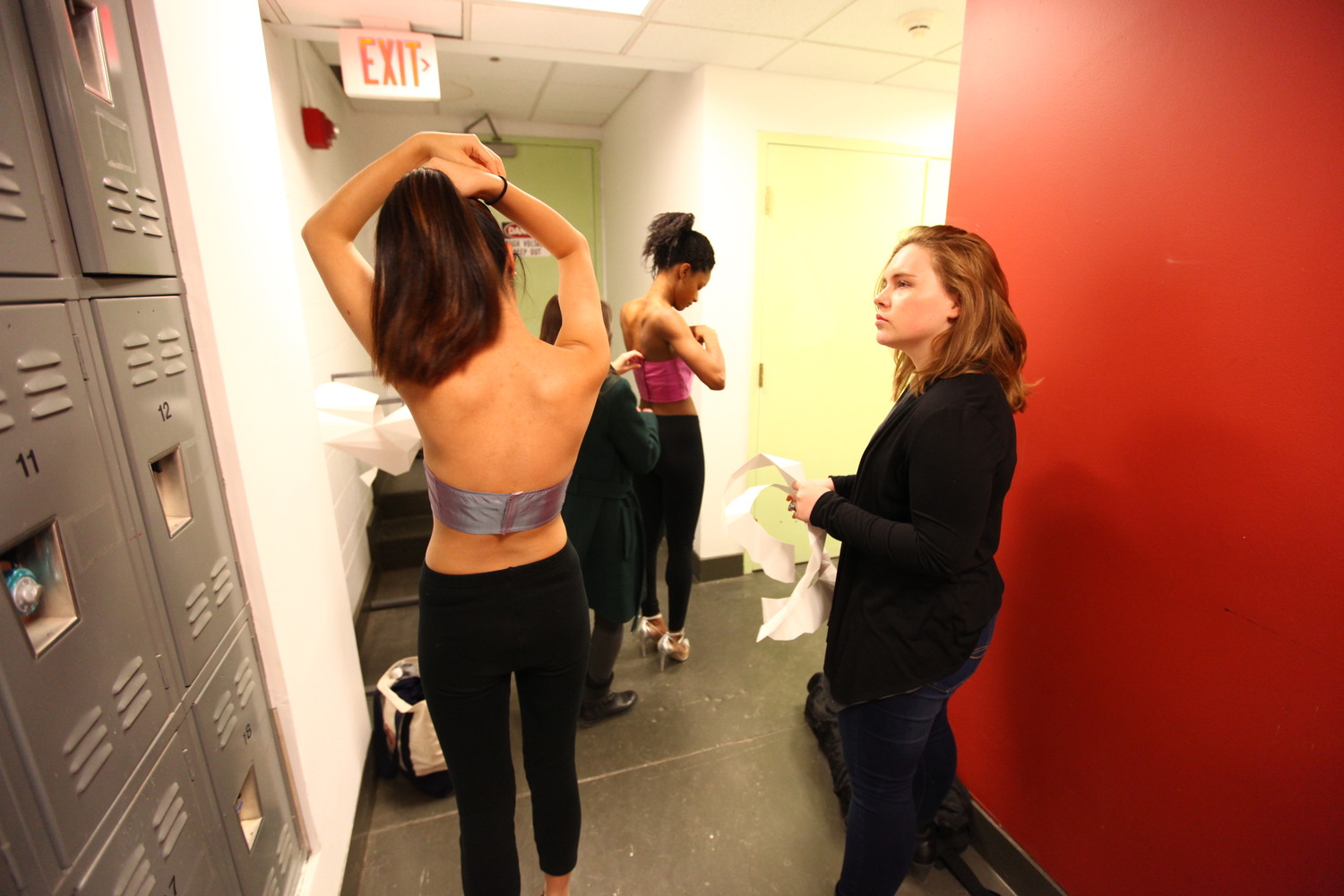
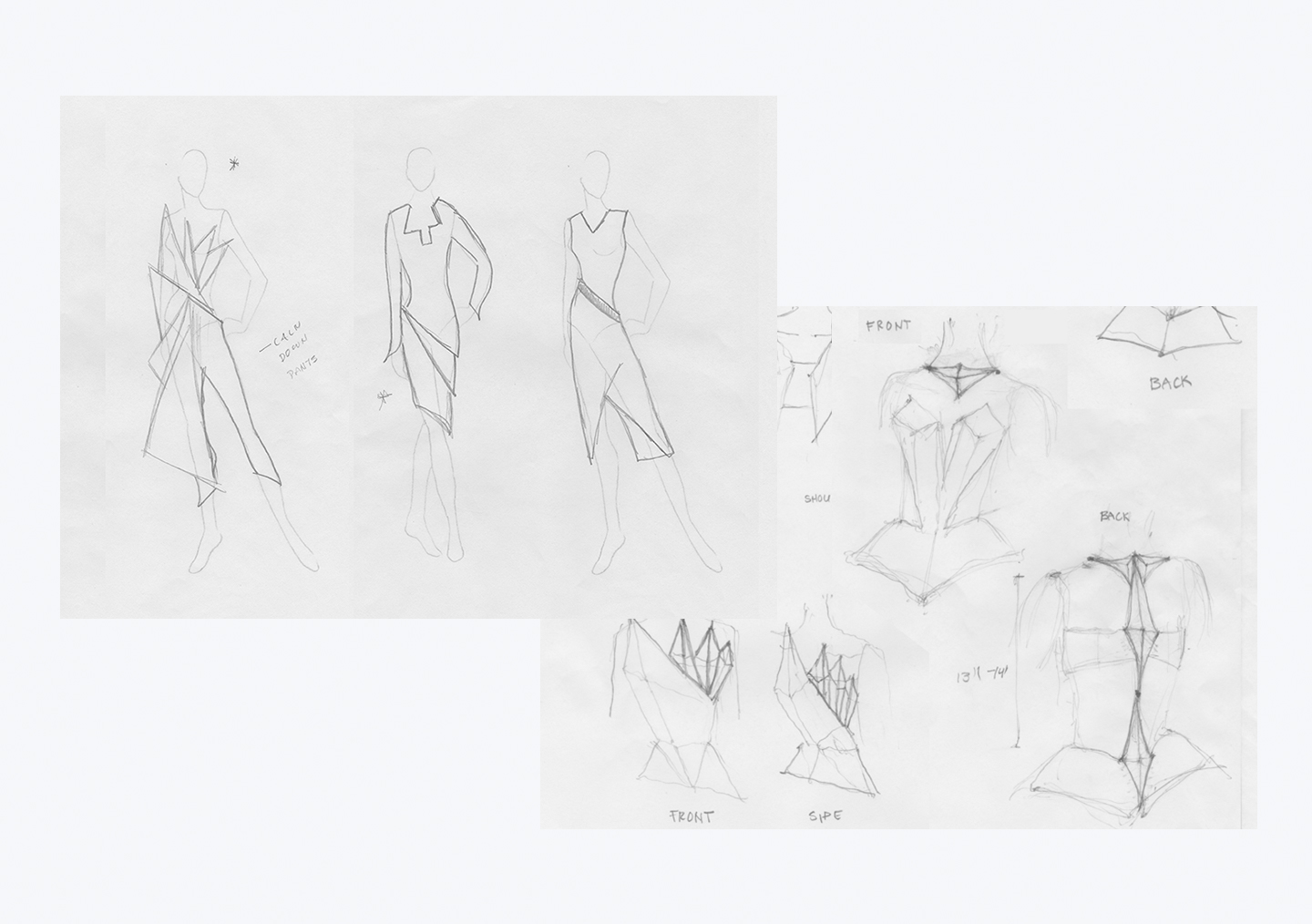
Initial sketches of look ideas and components we could 3D print.
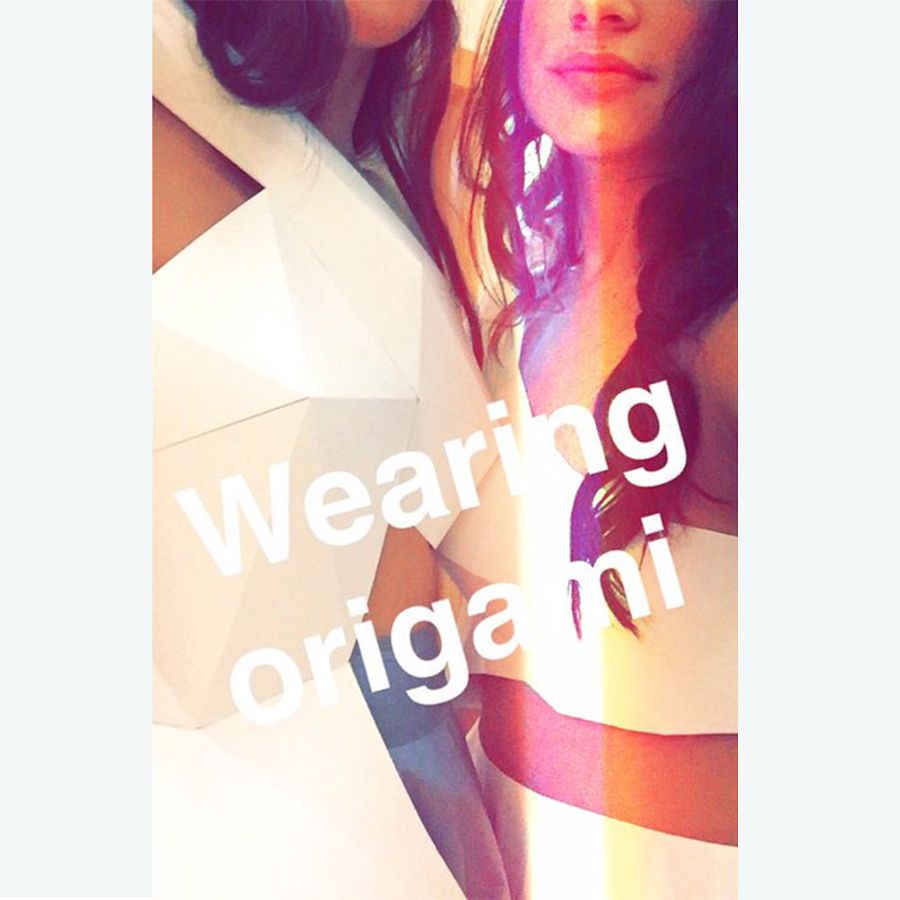
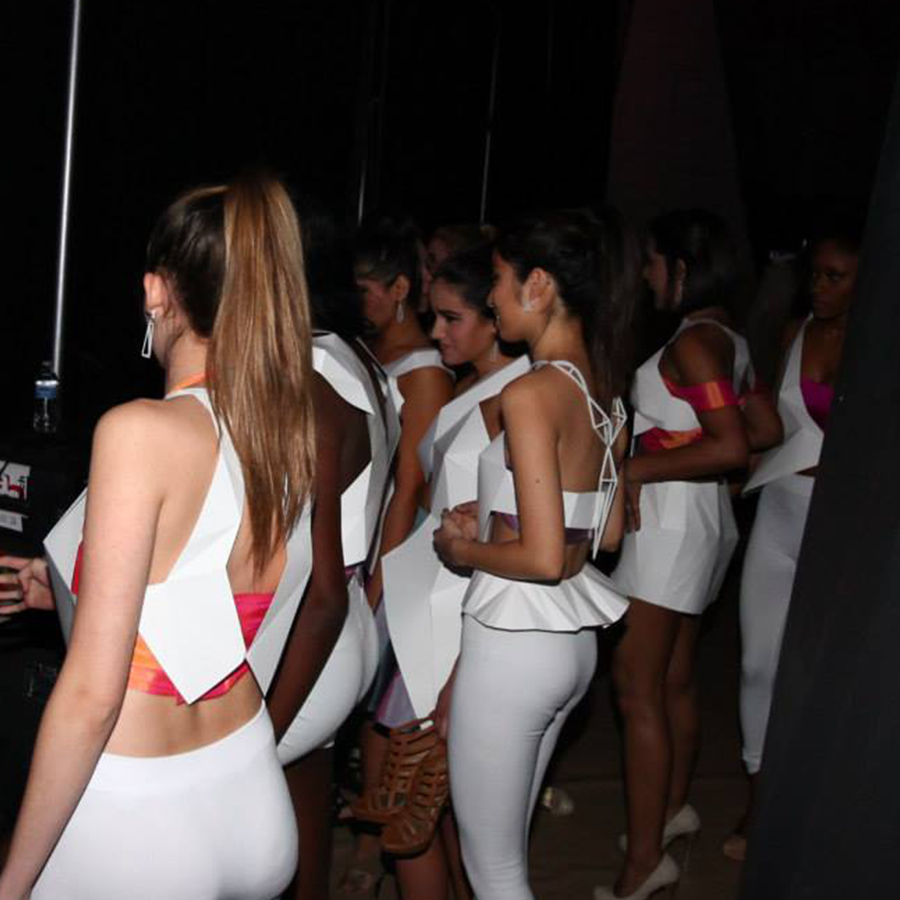
Some behind the scene images day of the show. #wearingOrigami